Equipped with the right sensors, unmanned aerial vehicles (UAVs) can help determine radiation levels after incidents in nuclear facilities as well as during routine monitoring.
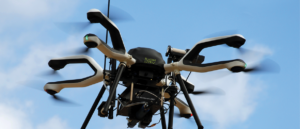
The Neo octocopter from FlyCam UAV. Neo is manufactured by Acecore Technologies in the Netherlands.
Over the last few years, drones have become a popular tool for a variety of applications at nuclear facilities, including both indoor and outdoor inspections and mapping. The industry is starting to trust unmanned aircraft systems (UAS) to improve safety for their workers, save time and cut costs—and that includes using the technology to detect radiation levels after incidents and during routine monitoring.
Drone companies like Charlotte UAV and FlyCam UAV have partnered with radiation instrument manufacturers to develop robust systems capable of carrying the necessary payloads. Some facilities are already using this type of technology for radiation detection (FlyCam has offered its DroneRad solution for about three years) while many others like Southern Nuclear, which is part of Southern Company, are just starting to look into its benefits.
“The idea is we’re going to eliminate the need to put lives at risk by using an aerial robot,” Southern Company UAS Standardization Pilot Corey Hitchcock said, noting Southern Nuclear has used UAS for a variety of applications since 2015 including containment inspection and mapping. “We’re looking to use multiple aircraft to determine the extent of the plume or the boundaries of the release.”
COLLECTING RADIATION LEVELS WITH TRADITIONAL METHODS
There are different ways radiation levels are collected, depending on the area in the facility. In containment, personnel responsible for monitoring health hazards at the facility survey areas to identify acute radiation zones, said Tony Cinson, senior technical leader—nuclear plant support nuclear sector for Electric Power Research Institute (EPRI). They typically use Geiger counter technology for these assessments, but also wear other detection measurement technology such as electronic personal dosimeters (EPD) and thermoluminescent dosimeters (TLD). Because of concerns of overexposure, it can be difficult for personnel to obtain measurements in certain places, such as confined spaces and areas at higher elevation.
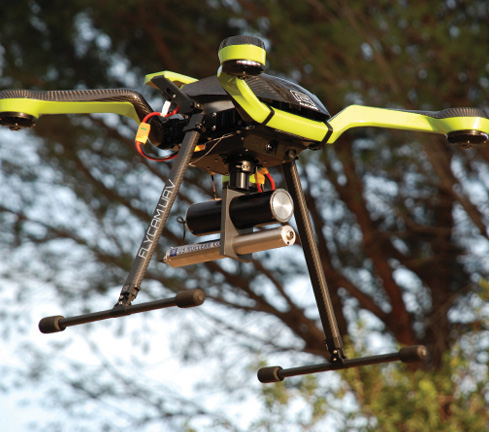
The Zoe is an all weather quadcopter from FlyCam UAV that features up to 40 minutes of flight time.
Area Radiation Monitors (ARMs) are also strategically located throughout the radiologically controlled area (RCA), Cinson said. These monitors are connected to alarming systems to alert personnel when radiation levels are nearing limits that aren’t expected during normal operation.
External radiation monitors are located at fixed positons outside the RCA, Cinson said, and in the neighboring communities, providing plant and emergency responders with information about the spread of contamination in the event of an accident. These sensors have their limitations, though, because they are fixed in one location and can’t provide a comprehensive radiation survey of the facility.
UAS AND VIBRATION
THE ELECTRIC POWER RESEARCH INSTITUTE (EPRI) AND CHARLOTTE UAV are working on another drone project that involves vibration imaging for indoor inspections of welds and other vibration sensitive assets.
This visual based (non-contact) methodology allows for detection and assessment of component and system vibration during operation, said Tony Cinson, EPRI’s senior technical leader—nuclear plant support. The principle of operation of the OptiVibe (by Allied Reliability Group) is to use high speed video to acquire data on systems/components and compare frame by frame and pixel by pixel to detect and quantify cyclic motion.
The system’s output is essentially a vibrogram that renders an image of the system with false coloring overlaid to signify regions of vibration detected, he said. Further analysis quantitatively results in an assessment of the frequency of vibration detected. This is similar to outfitting the component with thousands of accelerometers (one at every pixel within the image) to build a comprehensive view of the system’s motion.
“In relation to power plants, there are a number of pumps, valves, motors, bearings and small bore cantilevered piping systems that typically vibrate during use,” he said. “This inspection methodology can provide a precursor assessment to degradation before it becomes a significant issue requiring immediate attention. For example, if a small bore piping system is vibrating at a certain location, the location can be readily identified and restraints can be installed to minimize future vibrations that could induce mechanical fatigue cracking in a socket weld.”
This is typically done with a tripod mounted system that’s connected to a laptop. Working with Charlotte UAV, Cinson and his team were able to put the system onboard a customized UAS platform. For this to happen, the drone had to be large enough to support the payload, which includes a high speed camera, cinematography gimbal, an on board NUC computer, and wireless data transmission equipment.
The cinematography gimbal provided the necessary vibration isolation from the drone operation so high-quality data could be acquired. Flying a small modular computer, it was essential that the OptiVibe acquisition program could be executed and the large data files stored locally. Wireless communication was a key functional requirement, making it possible for the data to be acquired remotely and transferred without contact.
“The concept here was to develop a mobile vibration imaging platform that could remotely acquire data while either perched at a vantage point of the system, or, ideally, acquire data while in hover mode targeting the component of interest,” Cinson said. “As of today, the system is fully functional to acquire data from a perched vantage point as field trials identified we still have too much motion (drift) of the UAV in hover mode. The next phase plans to address this limitation by improving balance, improving the UAV platform, and enhancing stable flight controls. This includes making the necessary modifications to enable stable flight in GPS denied environments.”
THE BENEFITS OF USING DRONES INSTEAD
Drones can help acquire radiation levels during routine monitoring and after accidents.
“Using UAVs to detect radiation in a post-accident scenario would be extremely beneficial,” said Sam Johnson, technical leader—nuclear plant support for EPRI. “The systems would allow us to map the radiation levels within an area so we know where we can safely send personnel and where we can’t. UAVs flying through the air move faster than a person in a vehicle who has to follow the roads. If we have a pre-planned mission for a UAV to fly, there’s also a time-saving factor.”
Charlotte UAV recently began working with Mirion Technologies and RADeCO Inc. to offer this type of solution.
During an emergency, facility personnel are typically sent out in pairs to acquire data from the moving plume, said Keith Lovendale, President and CEO of RADeCO. One collects radiation levels while the other drives the vehicle. The information gathered is sent back to the plant so workers responding can compare the plume model to the actual dose rate. The model is created to determine how far and where the plume is going to travel.
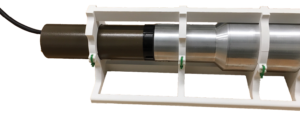
3-D MOUNTING BRACKET
Goldfinch Sensor Technologies and Analytics created a 3-D printed mounting bracket to hold a radiation detector to measure the levels and types of radioactive materials. The bracket was part of a proposal to show how a UAS could be used to map radioactive areas.
“The teams are sent out to areas based on wind direction and the plume models,” Lovendale said. “Once they get to the plume, they traverse across the plume to find the center, which is where they’ll find the highest radiation dose. They make notes of where the highest rate is and where there is no rate. They also might take air samples if there’s a ground plume situation.”
The challenge is, these teams can only collect a ground level dose rate. Drones can quickly and easily find the center with one employee and without the need to put anyone in harm’s way—collecting data these facilities never have been able to collect before.
“They can’t see where the true center of the plume is, which is elevated some distance above the ground,” Lovendale said. “With a drone, you can pull sample data from the center of the plume, which provides more accurate, useful information we didn’t have access to before. This data can be compared to the model so evacuation plans can be changed as needed.”
Charlotte UAV’s industrial X8 configured system, known as the RadKnight Duke, can be equipped with various radiation detection instrumentation to provide real-time radiological data through the Mirion Flight Control System and SPIR-Ident Software. As the UAS collects data, the user on the ground receives a live stream of a spectrum of colors and GPS tags that shows the strength of the radiation as well as a map of where it’s coming from, combining the onboard GPS data with the detector output.
Flying the UAS not only reduces radiation exposure levels for personnel and the man hours necessary to collect the levels, it also provides access to and maps of areas people and cars simply can’t reach. Many nuclear facilities are located in rural areas, which makes it difficult to get to the plume as the wind carries it away from the plant, said Kip Kelley, a technical sales engineer for Mirion Technologies.
The FlyCam UAV platforms, the Neo Octo Drone and the Zoe Quad Drone, are all-weather systems that can carry two radiological sensors—a plume sniffer and an alpha beta gamma search tool for fixed sources other than a plume, both from US Nuclear Corp. The sensors provide radiation levels in real time, eliminating the need for personnel to put on hazmat suits and walk into potentially dangerous situations.
While they can’t talk about specific use cases, the systems are typically deployed to survey fixed points and determine if radioactivity at those points has changed, said Bob Goldstein, CEO of US Nuclear Corp. Such surveys are completed about four times a year. Customers are also interested in quantifying radioactive plumes, determining where they’re coming from and where they’re going. Another potential use is to check for gases coming out of the stacks at these facilities.
“Right now the radioactivity levels in those plumes is determined by computer simulation. There’s no measurement done,” Goldstein said. “You can take the drones up the stacks and physically locate the plume and evaluate the activity in the plum and which way it’s going to go, which is a great advance from what they currently do. Now workers hold a detector at waist level and point it up in the sky, hoping to see the radiation in the plume. This new method is going to work better.”
Because there isn’t a central spent fuel repository in the U.S., plants are required to store spent fuel on-site in dry cask storage containers
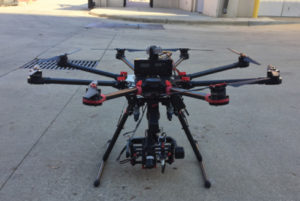
DRONES AND EPRI
EPRI sees the value in using drones for a variety of applications in nuclear facilities, including radiation monitoring and detection as well as asset inspection.
located on independent spent fuel storage installation (ISFSI) areas, Cinson said. The ISFSIs require walk downs to visually verify the vent locations on the dry cask storage containers are not blocked, which would prevent natural cooling and lead to problems.
“These walk downs can pose safety risks to personnel and can easily be automated by UAVs,” he said. “Additionally, detailed 3-D surveys can be conducted using UAVs to map and monitor the low level radiation areas in and around the ISFSI sites that can eliminate the need or reduce the magnitude of costly concrete berms erected to keep off-site radiation doses to a minimum.”
THE CHALLENGES
Of course there are various challenges that come with using drones to detect radiation. The first is the size of the sensors and the drone. The payload must be light enough to fly on a UAS that’s small enough to safely travel in the facility and to access tight spaces and confined areas.
Goldstein met that challenge by using thin aluminum or carbon fiber for all mechanical parts rather than steel or brass. He got rid of the lead collimators used on other radiation equipment and also plan to switch to smaller, denser scintillation crystals for the “search tool” detector.
“The first thing to do is make the sensors small and lightweight so they can go on the drone without overpowering them,” he said. “And then you need a quick change. We developed a quick change system so it takes just a few seconds to change from one detector to another by clipping in and plugging it in to a different wire and cable.”
When Goldstein came to Jeri Donaldson, CEO of FlyCam UAV, and her team with radiation detection devices and the idea to fly them on the drone, it didn’t take long for them to figure out the best way to mount the sensors onto the systems. The company has 20 to 25 sensors that detect 18 different chemicals. The main challenge was determining how to get the right data.
“There are so many different levels of contaminant and strength of contaminant,” she said. “You have to decide what levels you want to detect and how fast or slow you want to fly.”
Then there’s navigation, Johnson said. It’s difficult to fly drones through indoor, GPS-denied environments. Not only that, certain areas of the turbine building are sensitive to radio interference, Cinson said. UAS need to be designed to eliminate the risk of tripping the plant offline.
To ensure personnel flying the UAS and other employees are safe, there also must be ways to keep the UAS clean and free of contamination.
“One of the worst scenarios would be if a UAV is rendered inoperable during a mission and cannot be easily retrieved,” Cinson said. “Tethered operation could provide a solution, but then access limitations come into play. Considerations must also be given to contamination prevention of the UAV.”
Not all the challenges are technical. Before drones can become common tools used in nuclear facilities, workers must not only accept the technology, but learn how to use it, said Matt Torma, business development manager for Charlotte UAV. Training is key to ensuring UAS can safely and effectively gather the necessary data. That means establishing comprehensive drone programs in these facilities and having enough Part 107 pilots to complete the required missions.
“The UAS industry is still technically in its infancy and it seems like there’s something new to be added every week,” Donaldson said. “We’re finding a lot of companies have not instituted a proper UAV program or protocols so our challenge is bringing them up to speed. We’re really trying to encourage companies to go down that path and establish programs. They’ll be much more successful with their purchase, and that reflects better on everybody.”
UAS AND GROUND VEHICLES
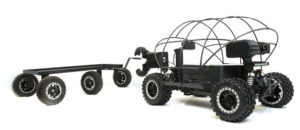
DESTRIER– LR
The medium sized Destrier– LR is an all-terrain autonomous vehicle that can carry a variety of payloads on its main body or towed by a trailer.
Ground vehicles can also be effective during an emergency response at a nuclear facility, said Matt Torma, business development manager for Charlotte UAV. Once the plume is gone and a UAS has been used to detect radiation levels, a system like the Destrier—LR, a medium-sized all terrain, all-wheel drive vehicle, can continue to collect data. The autonomous vehicle can cover miles while carrying various payloads on the main body or towed by a trailer. It also can be equipped with a self-righting roll cage to traverse challenging areas. The Rover uses the Mirion Mission Control Software, which is also used to operate the RadKnight UAS.
“You want to use aerial systems right away and then ground vehicles,” he said. “After a couple days all the debris from the plume has fallen out and will get on the ground. Aerial vehicles aren’t great at surveying the ground. A ground vehicle is a much more efficient tool for these surveys and can run for a longer period of time. You also can put a bigger payload on them.”
The ground rover was developed because customers were constantly
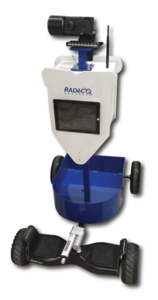
BUDDY THE GROUND ROBOT
Buddy is a semi-autonomous ground robot for use in hazardous areas. The vehicle is designed to be “plug and play” with various Mirion radiation detectors and cameras.
asking about a system that could stay on the ground and loiter, said Walter Lappert, an unmanned systems engineer for Charlotte UAV.
The vehicle has front facing cameras (visible light and thermal), rear facing cameras and now a set of two radiation detectors mounted on. It operates via GPS waypoints or manually. Like the UAS, it livestreams what it sees back to the operator. A second person can put on virtual reality googles to see all the data as it comes in, offering another perspective.
Torma sees this being used to monitor for radiation in shipping and receiving areas. It also can be used for other applications, including infrastructure inspections and security walk downs, much like the UAS.
OTHER USES FOR RADIATION DETECTION
Detecting radiation and harmful chemicals via drone can be beneficial in other areas, including Border Patrol and military applications. It also has the potential to detect groundwater contamination near nuclear weapons facilities and coal-burning power plants.
Mark Roberson, president of Goldfinch Sensor Technologies and Analytics, worked with First Flight Venture Center’s Hangar6, an advanced prototyping facility, to create a 3-D prototype of a custom, lightweight bracket that is designed to integrate the company’s radiation detector into the airframe of a small UAS. Equipped with the proper sensors, the UAS can be used for environmental monitoring at U.S. Department of Energy (DOE) facilities that once developed nuclear weapons. The DOE recently listed Goldfinch Sensor among companies it intends to negotiate a contract for reward through the Small Business Innovation Research (SBIR) and Small Business Technology Transfer (STTR).
Through the project, which is still in its very early stages, Roberson plans to develop a drone sensor to monitor low level, background radiation, he said. While the radiation levels present at these sites won’t lead to immediate damage, even small levels could cause problems over time by contaminating drinking water or the food supply.
“We want to do spatiotemporal analysis of residual radiation,” Roberson said. “They already know there’s radioactive iodine-129 present on the site and which areas it’s elevated in. They need to know how it’s changing over time.”
Rain storms can alter the patterns of the low level radiation at the top, but it’s not easy to predict how. Monitoring the sites and feeding the information back into a risk analysis system will help. And because the drone will be operating at a DOE site, security measures have to be very tight, Roberson said. The drone also must be robust and reliable.
“It has to integrate location and time along with the readings from the scintillator,” Roberson said. “If the scintillator is flying along and says it sees so much iodine-129 and leftover 131 along with some naturally occurring radioactive potassium, it creates a map that shows it saw this much of certain materials at this location and this much at this location. The map will evolve over time, especially after heavy rains. This will provide input into policy decision making. The technology offers the possibility of providing targeted quantitative assessment of the change in radiation distribution, which would guide remediation efforts.”
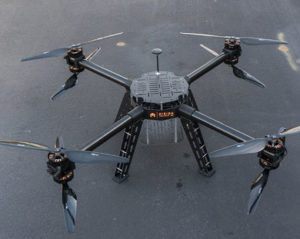
RADKNIGHT DUKE
This medium lift drone can carry various radiation detection payloads.
Roberson hopes to be under contract with the DOE and beginning the development process soon. If that happens, the first phase will last about nine months with the goal to show the feasibility of the solution. There’s also the possibility of a second phase if the first is successful.
A BRIGHT FUTURE
Radiation detection and monitoring is just two of many drone applications the nuclear industry will continue to explore. The possibility of using drones to inspect a variety of assets to check for leaks, cracks and other issues is generating a lot of interest, as are more security-related applications that help keep these facilities and their workers safe.
While a UAS certainly isn’t the only tool, it’s becoming a more effective tool that the nuclear industry is trusting more and more—a trend experts expect to continue as the technology evolves and employees become more comfortable operating these systems.
“The UAV industry is growing at a rapid pace,” Johnson said. “The nuclear industry is taking note, and looking to see how they can incorporate these technologies into their plants to make them safer, more efficient and more cost effective.”