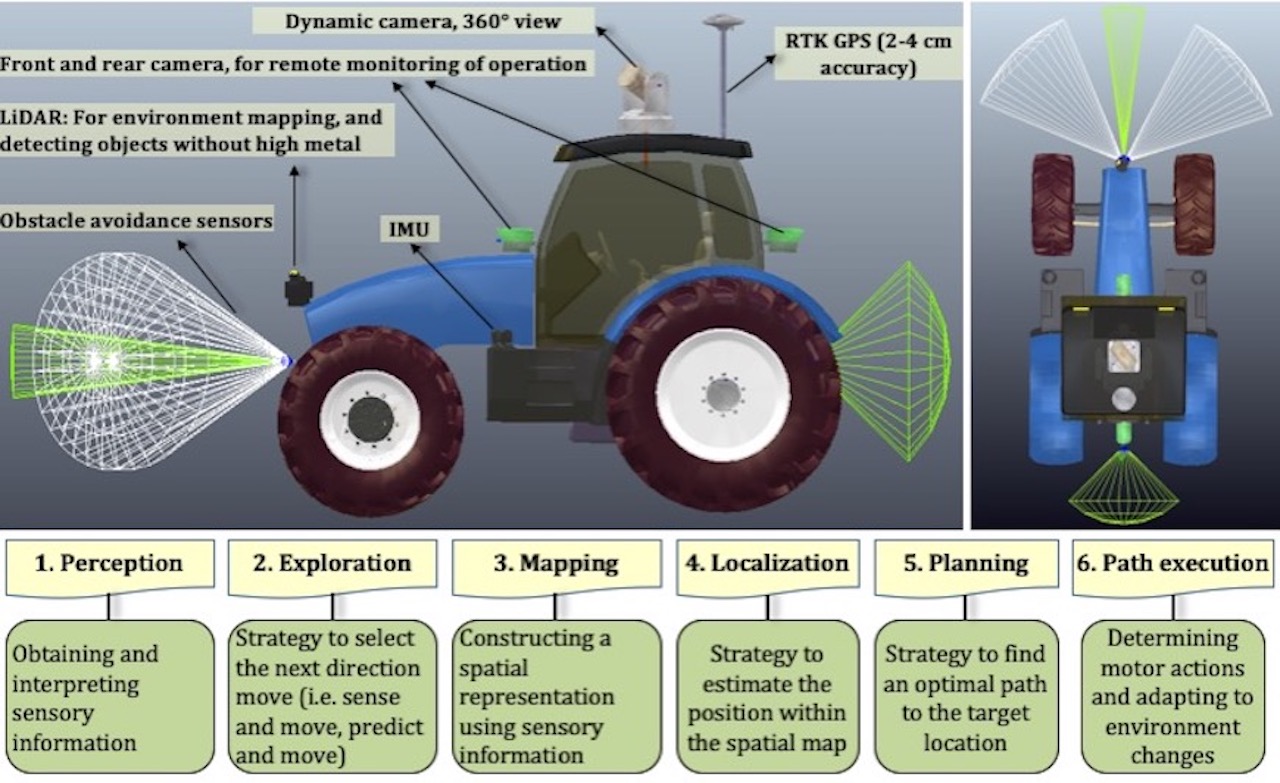
Sunbot, courtesy Redmond Shamshiri
An autonomous electric tractor-mower combination senses the environment, navigates in row orchards, and identifies and avoids obstacles. The SunBot project will improve labor productivity and cost efficiency in bush berry cultivation by automating weed control.
This article was originally prepared for the February/March 2020 issue of Inside Unmanned Systems magazine, with a focus on Precision Agriculture, but unfortunately had to be dropped at the last minute for lack of space.
by Cornelia Weltzien, Technische Universität Berlin, and
Redmond R. Shamshiri, Leibniz Institute for Agricultural Engineering and Bioeconomy
The production of bush berries such as blueberries, raspberries and currants is under increasing economic pressure, particularly because of the labor-intensive, costly cultivation measures required for harvesting. A shortage of skilled workers and rising wages are forcing farmers to innovate.
In berry orchards, regular mowing between the rows reduces plant competition and provides open space for cross-row ventilation, which in turn allows orchard hygiene and health. This holds even more true in organic berry farming, where frequent and regular care is essential to improve aeration between plants, minimize potential disease and prevent loss of income.
Regular mowing, however, is a highly repetitive, resource- and labor-intensive task. Coupled with labor cost and shortages, this has led to sub-optimal care measures and orchard conditions. In turn, lack of proper orchard nursery management, especially in organic farming, negatively affects both yield and quality: profitability and productivity continue to decline. Increasing the number and frequency of actual nursery management practices requires reducing the associated costs, work force and resources.
The aim of the SunBot simulation is to develop technologies for autonomous and emission-free mowing operations in orchards. The name SunBot emphasizes the unique features of the technical innovation: “Sun” stands for the coupling of electric drive with regenerative (solar) energy as a zero-emissions solution, fed by photovoltaic power. “Bot” stands for robot, denoting the autonomous tractor that increases labor productivity.
Why electric? Many farms produce electricity from renewable sources (biomass, geothermal, hydroelectric, solar and wind power), which is economically attractive for decentralized on-farm use. Efficient battery technology is becoming available and suitable for use in compact tractors. Increasingly stringent demands for reducing noise and exhaust emissions also drive the development of electrical systems.
Frequent mowing will have a positive effect on the yield and fruit quality of the fruit. This kind of automation could even facilitate mowing and other forms of cultivation during nighttime.
Concept development
The first development phase in this German-based project included preliminary studies and experiments to construct a functional model of an autonomous electric tractor with an innovative efficient electric mower that could sense the environment and navigate without human input. The system must also detect and respond to avoid both stationary and moving obstacles.
Safety
The safety system is closely linked to the sensor concept for autonomous navigation and steering. Both concepts use visual and optical sensors for object and environment detection, as well as GPS, orientation and acceleration sensors for position determination in space. Other sensors check signal transmission and technical system parameters such as overheating.
The sensors used for autonomous navigation and steering also provide safety-relevant information. For example, in case the sensors signal “obstacle on the right,” an evasive action should be initiated. The system should either move to the left or stop, depending on whether a hazardous situation is detected.
Navigation
The orchard environment is challenging for autonomous navigation. Berry bushes (Figure 1) are medium-sized woody fruiting plants that are cultivated in row-spaces between 1.5–2.5 meters. The tractor should be able to navigate autonomously between the rows with the accuracy of 5–10 centimeters from the plants while maintaining an ideal speed of 5–8 kilometers/hour. This poses an extremely challenging task due to the structural dynamics of the growing orchard, including land topology and the variation in planting systems.
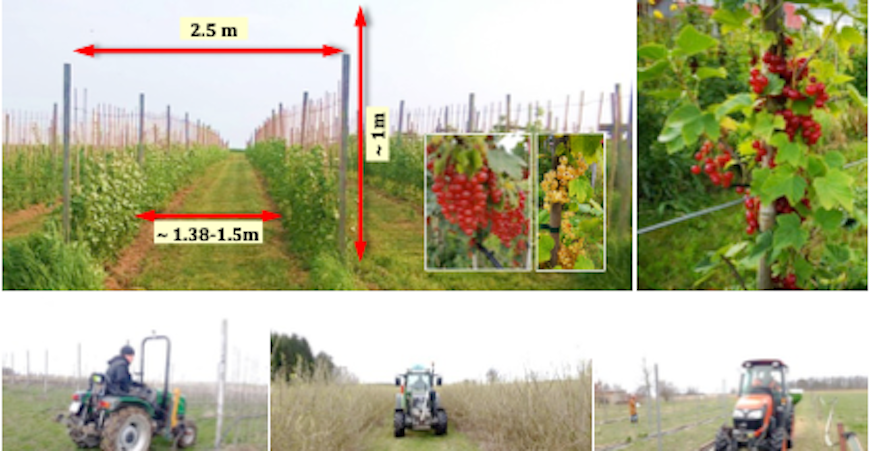
Figure 1 Shrubbery orchards: dimensions and environmental variation (Source: Weggun)
To overcome these challenges, a simulation-based development process initiated the project. Field visits collected preliminary data collection with high-accuracy real-time kinematic (RTK) GPS to feed the Virtual Robot Experimentation Platform (V-REP) that interfaced with the Robot Operating System (ROS) for testing different sensors in an hardware-in-the-loop approach with control algorithms on a full-scale simulated tractor and orchard model.
Optimal positioning of the sensors on the carrier vehicle is determined with the help of simulations. The overall objectives are reliable and safe navigation and steering in the system (lane, turning circle, etc.). Obstacles such as fruit boxes or uneven terrain must also be factored and tested in the simulations. Currently, the first automation tests are being carried out on model vehicles.
Simulation Environment
ROS is a flexible open-source middleware that provides services, libraries and tools for developing different robotic applications. Installation details and basic configuration of the ROS environment, as well as installation and configuration of packages such as V-REP/ROS bridge, and the details of several mobile robot and manipulator package are available in the References section of this article.
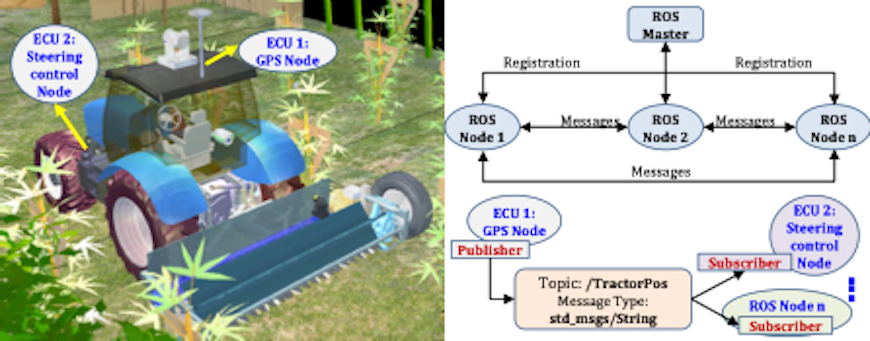
Figure 2 Development of a full-scale simulated model of an electrical tractor and orchard for accelerating the experiments with different sensors and control algorithms.
In the software layer, ROS was installed on an onboard computer called ROS Master that can be connected to multiple computers or electronic control units (ECUs). A schematic diagram of ROS file architecture and principle of nodes communication system appears in Figure 2.
In the hardware layer, a distributed system shown in Figure 3 was designed for modular communication between different ECUs, controllers and actuators via the CANBUS and an ethernet connection. This structure enabled creation of a modular network of nodes dedicated to subset computations with an organized communication between them.
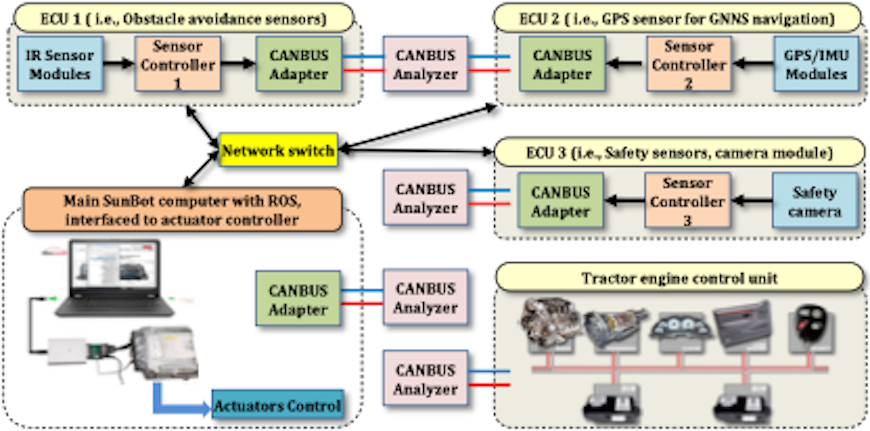
Figure 3 Schematic of the ROS-based distributed framework for modular communication between different ECU, controllers and actuators via CANBUS and Ethernet.
Robotic libraries such as frame transformation and motion simulation were shared with all nodes to simplify the computation process. Implementation of the prototype obstacle avoidance board was realized on a lab-scale e-tractor for experimenting different autonomous navigation algorithms. In this scheme, each ECU is responsible for processing its sensor data and sending the final command to the onboard computer. The onboard computer then processes and compares all command signals from different ECUs and sends out the proper command signals to the actuator control for driving the tractor.
Simulation for acceleration
The simulation approach converted native data streams from various sensor inputs (e.g. GNSS, LiDAR, laser and radar) into usable information within the command-and-control system for experimenting with autonomous navigation while avoiding moving or stationary obstacles in the orchard. This approach provided a safe, fast and low-cost experimental platform for development, testing and validating control strategies and algorithms. The main elements of the simulation scenes in this project were:
- mesh files representing plants, tractor, environment, obstacles
- software including V-REP, ROS and MATLAB
- algorithms including image processing, inverse kinematics, minimum distance calculation module, visual servo control, Ackermann steering (linkages arranged to trace circles of different radii), path following and obstacle avoidance algorithms.
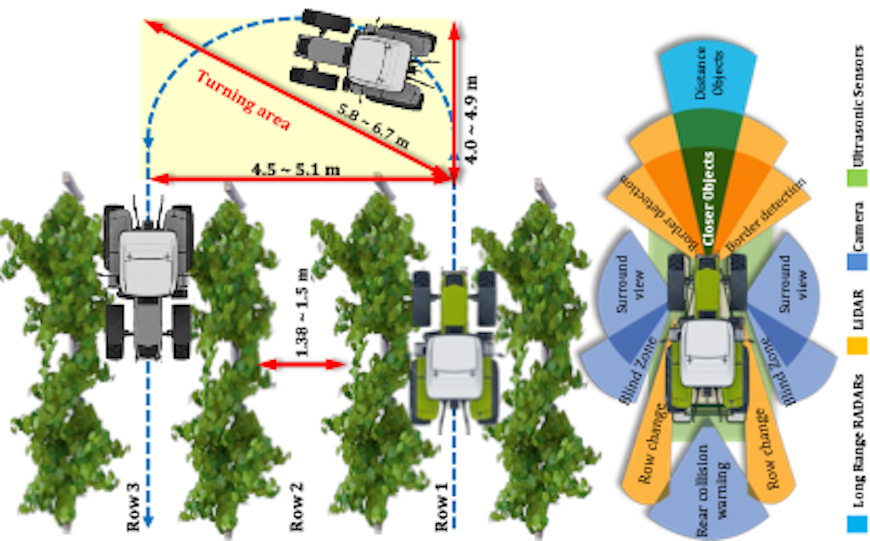
Figure 4 Schematic view of the row-end turning pattern for the SunBot e-tractor in berry orchards using sensor fusion.
As the first step, different sensors and their positions on the tractor were evaluated in V-REP for experimenting with a possible row-end turning pattern (Figure 4). In the next steps, an operational simulated electrical tractor with front and rear linkage mechanism and Ackermann steering was created. In addition, a simulation orchard with scaled planting system and random obstacles was designed. Message exchange between the objects in the simulation scene and in the real-world was carried out via ROS.
Figure 5 shows simulation scenes associated with different scenarios involving tractor, mower, orchard, and obstacles, including:
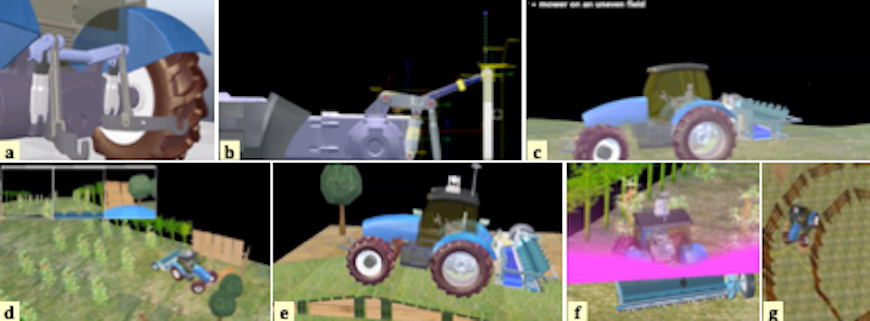
Figure 5 Different scenes of dynamic simulation studies: tractor, mower, orchard and obstacles.
- front and rear linkage for mower attachment (a,b)
- dynamic interaction of tractor and mower on uneven field (c)
- row-end turning with the tractor while driving in reverse (d)
- stability analysis of the tractor and mower when introduced to large step changes from the field (e)
- environment mapping using LiDAR (f)
- testing RGB camera, proximity sensors, and laser beams for obstacle avoidance within the plants rows (g)
The Row Ahead
The SunBot project automates an electric tractor powered by solar energy sources for resource-efficient berry cultivation. Field trials are being scheduled and, when completed, SunBot will perform autonomous navigation within highly dynamic and unstructured agricultural environments. The SunBot tractor should be able to respond to objects and obstacles in the environment. In the conceptual phase of the project, a distributed ROS-based framework was designed for communication between the tractor ECU, as well as interfacing with the main on-board controller in a modular approach. Using V-REP and ROS simulation, it was shown that the approach offering standard features such as hardware abstraction, low-level device control, implementation of commonly used functionalities, message-passing between processes and package management can significantly increase the development speed.
The use of the smart system will be tested in practice in raspberry, currant and blueberry orchards.
The framework made it possible to develop code and applications with minimum effort that will be shared and used by any sensors or actuators on the tractor. Additional simulation studies tested and validated different sensing and control strategies and tuned the algorithms. The concepts used in the studies address solutions for environment mapping, localization, obstacle recognition and path planning of a tractor driving inside berry orchards.
Acknowledgment
This project is funded by the European Innovation Partnership‚ Agricultural Productivity and Sustainability (EIP-AGRI) program through the European Agricultural Fund for rural development (EFRE).
SunBot is coordinated by the Leibniz Institute for Agricultural Engineering and Bioeconomy (ATB) with partners Bauernhof Weggun, Biohof Schöneiche, Obsthof Neumann, VKR, ESM, HYDAC Software, MCE, HNEE, HSD.
The research on which this article is based was first presented at Agritechnica 2019, Hanover, Germany.
Authors
Cornelia Weltzien has a Prof. Dr.-Ing. Degree and is a researcher in future agricultural technology with the Leibniz Institute for Agricultural Engineering and Bioeconomy.
Redmond R. Shamshiri is director at Adaptive AgroTech Consultancy International. He received a Ph.D. in biosystem engineering from the University of Florida.
Electrical Tractor Specification
The project requires a universal two-wheel drive orchard tractor with all-electric drive with minimum drive power of 20–30 kilowatts that operates on a lithium ion battery. The total weight should not exceed 2,500 kilograms and overall width falls between 1.2–1.35 meters. The tractor should have front and rear Category 1 three-point hitches and an Agricultural Industry Electronics Foundation (AEF) power connector to drive double-blade mower (400 kilograms / 10 kilowatt). The tractor communication protocol is based on CAN-BUS. It features an interface for autonomous driving control signals (steering, speed, brake, and machine condition information) using a CAN-BUS proprietary protocol, and an ISO-BUS protocol (ISO-11783 standard) for data exchange between the tractor and mounted attachments.
References
- Bouchier, “Embedded ROS [ROS Topics],” IEEE Robot. Autom. Mag., vol. 20, no. 2, pp. 17–19, 2013.
- R. Shamshiri et al., “Research and development in agricultural robotics: A perspective of digital farming,” Int. J. Agric. Biol. Eng., vol. 11, no. 4, 2018.
- R. Shamshiri, I. A. Hameed, M. Karkee, and C. Weltzien, “Robotic Harvesting of Fruiting Vegetables: A Simulation Approach in V-REP, ROS and MATLAB,” in “Automation in Agriculture-Securing Food Supplies for Future Generations,” InTech, 2018.