At the intersection of drone autonomy and digital transformation, innovative approaches and integrated systems are shaping the future of essential industries—enhancing intelligent operations and customer experiences.
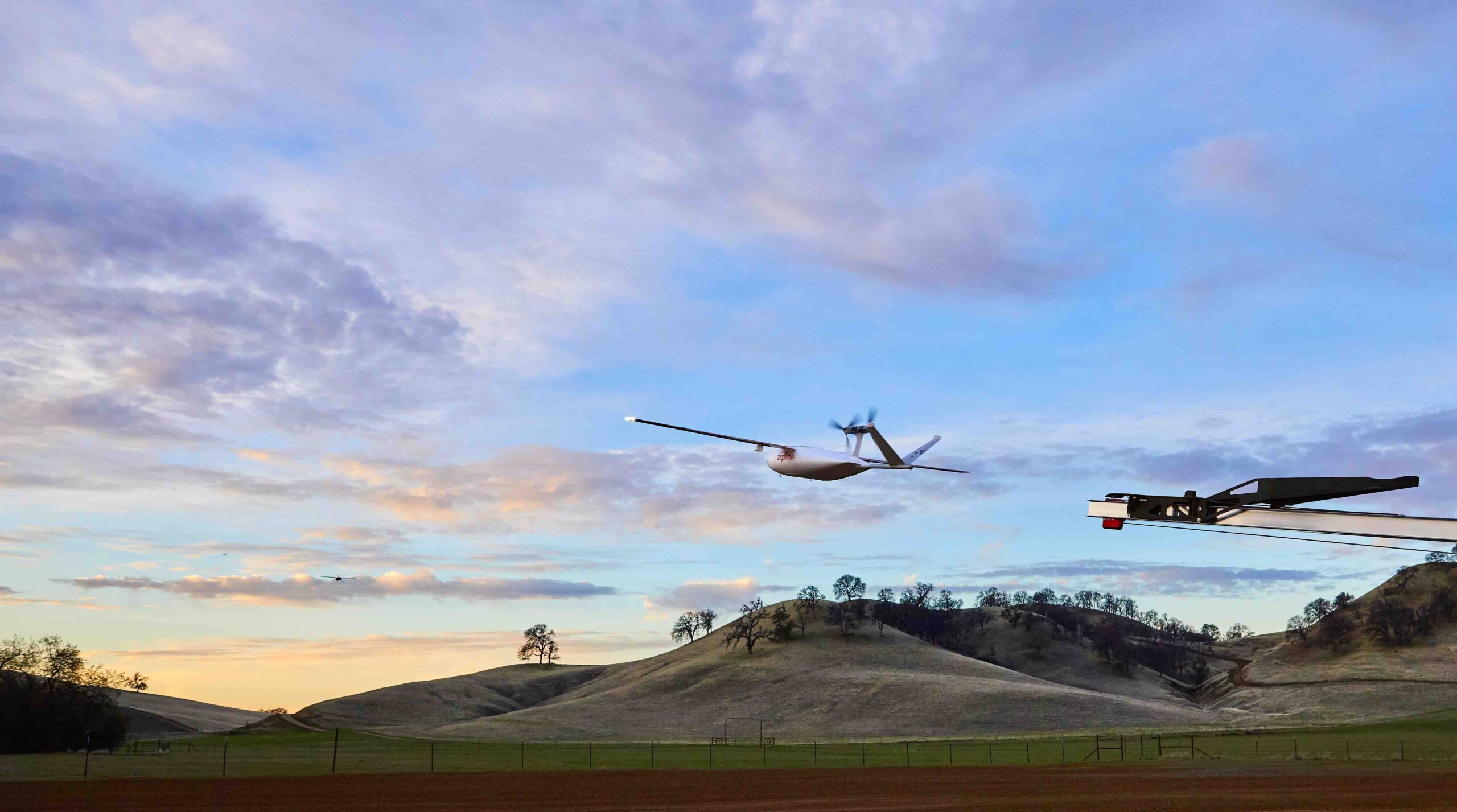
Strategy consultancy McKinsey defines digital transformation as the “process of developing organizational and technology-based capabilities that allow for continuous improvements to customer experience and lower costs; and over time sustain a competitive advantage.” As the exponential growth of digitization impacts every industry sector and market segment, drone-centered autonomy provides a vital benchmark for digital transformation in action. These platforms serve as a leading indicator of digital transformation’s impact—orchestrating digital tools to transform business models.
Autonomous navigation and AI-enabled predictive analytics are examples of how smart platforms synthesize their surrounding environments and learn at scale. Acceleration toward integrated technology platforms with UAS at their core grants OEMs and drone service providers an unmatched opportunity to create effective bespoke solutions driven by customers’ most pressing needs.
Weaving each component of a platform together while steadily decreasing the need for direct human intervention orchestrates the discrete tools into integrated, smart platforms. Inside Unmanned Systems discussed adoption and advances in capability sets with a range of practitioners in the field. Here, we dive into illustrative operational examples of drone autonomy driving integrated platforms that can inform, trigger—and independently perform—the best next action in the field.
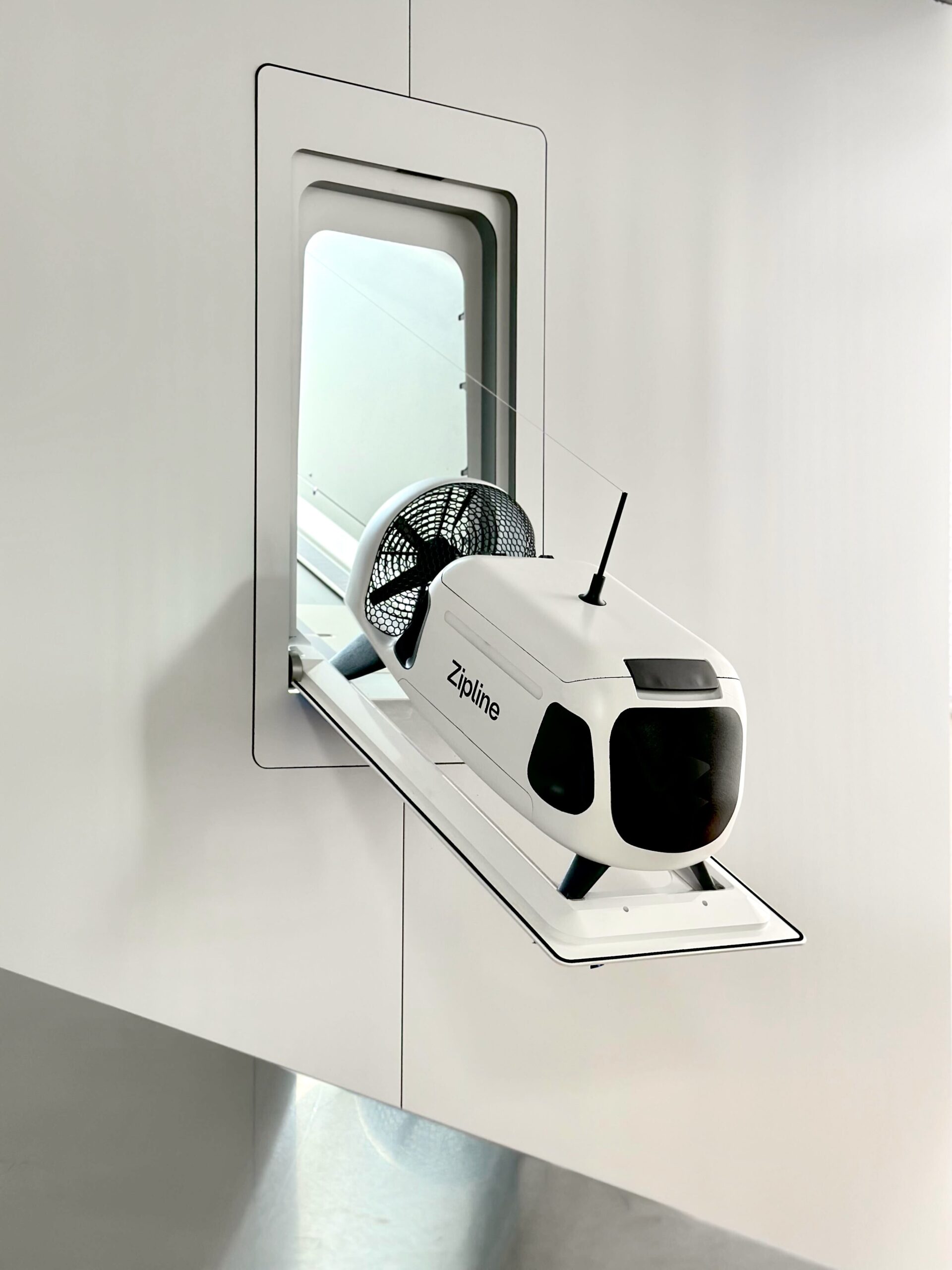
Autonomous Droids Performing Urban Deliveries
In the rapidly evolving landscape of drone delivery, Zipline stands out for its use of autonomous technology to enable the future of urban deliveries. Juan Albanell, head of system test engineering at Zipline, offered a glimpse into the company’s operational advancements and the future trajectory of its drone and droid systems.
Zipline’s initial venture into autonomy was through its Platform 1, designed to autonomously navigate from distribution centers to specific delivery points, mostly used in rural areas. Albanell said, “It is able to navigate without needing any user input,” by leveraging GNSS and IMU navigation systems coupled with a detect-and-avoid system to autonomously identify and circumvent obstacles.
The company is further developing Platform 2, aimed at bringing autonomy to urban settings. “We have a perception system as well to better facilitate the navigation,” Albanell noted, underscoring the adaptation for densely populated areas. The introduction of perception systems alongside GNSS and IMU navigation extends the drones’ navigational capabilities, crucial for the complex environments of urban landscapes.
A notable innovation in Platform 2 is the droid system, which Albanell described as capable of precise positioning for deliveries. “It can very accurately position itself to wherever the customer wants the package to be delivered.” This precision is required in urban areas, where delivery accuracy is crucial. The combination of IMU/GNSS navigation and perception systems enable the droid to navigate and avoid obstacles autonomously, showcasing the advanced autonomy Zipline aims to achieve.
The foundation of Zipline’s advancements in drone technology is a rigorous testing and prototyping regimen. Albanell leads the company’s testing approach, including extensive in-flight testing and simulations that mimic real-world conditions. He explained, “We’ve had many
vehicles flying, tens of vehicles flying around the same airspace, deconflicting between each other,” highlighting the autonomous capabilities of the drones in managing flight paths and priorities.
Zipline’s approach to scenario planning and testing is significantly data-driven, informed by a vast repository of flight data from a million deliveries. “A lot of the scenario definition and the way that we plan testing campaigns is very informed by past data,” Albanell explained. This data informs the development of specific scenarios to test, ensuring the drones are well-prepared for real-world operational challenges.
Albanell added, “when we do FMEA [Failure Mode and Effects Analysis] we basically determine things that could happen in-flight that we believe might have specific ‘corner cases’ for the sensor set, for example. And then we spin up software mockups that allow us to easily test different modules of the software with flight simulations. The software that is flying in-the-loop cannot tell that it is not actually flying.”
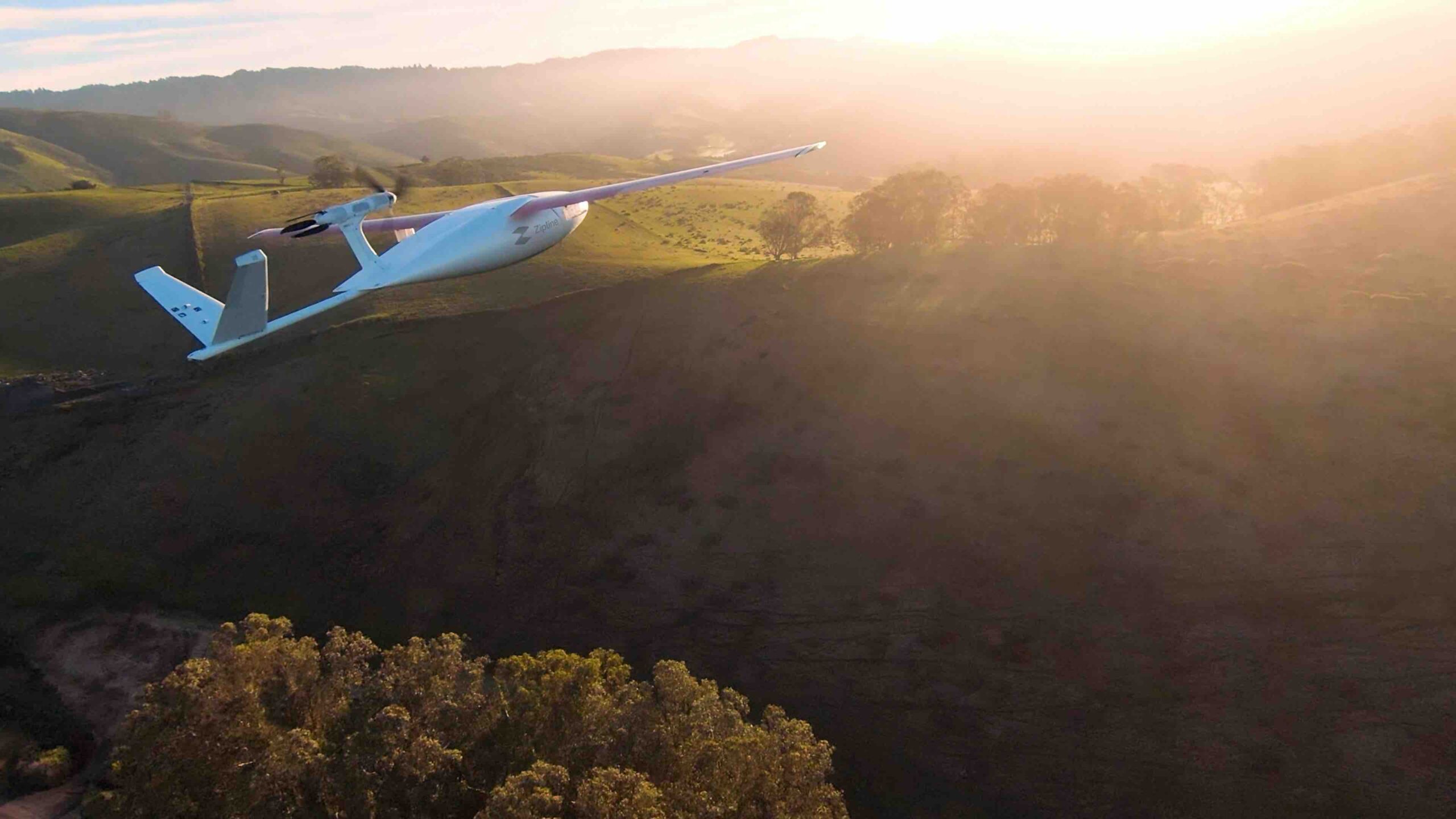
Always-On Scenario Planning
In a sense, the system is functionally running all the time, whether in a simulation or an actual flight. Albanell added, “About half the time we spend is actually developing new things for our hardware and software, and then the other half is testing. More than half of our time, sometimes, is spent on test development. Because you can have something that nominally works. But nominal is not what hardware interfaces with, right? The real world is not nominal, it is going to rain, it is going to be windier than you expect, a bird will fly by, there will be other aircraft in the field that you didn’t expect. We have to test for all of these situations.”
Albanell explained that an “a-ha moment” in scenario planning is the importance of volume. “The diversity of your scenarios is so important. The biggest thing we’ve learned is to make your scenario builder as flexible as possible, so that you and other people can easily add things in the future.”
Looking beyond the immediate technological challenges, Albanell points to the importance of internal autonomy in manufacturing and testing processes. He articulates the need for scalability to meet customer demand, indicating, “A big part of us meeting demand is going to be autonomy at a layer removed from the customer, at the manufacturing level and the test execution level.” This perspective highlights Zipline’s comprehensive approach to implementing autonomy, extending beyond drone flight to include manufacturing and operational processes.
As Zipline continues to develop its autonomous drone delivery systems, the insights shared by Albanell shed light on the complexities and innovations driving the future of urban logistics. With a focus on enhancing navigational capabilities and operational efficiency, Zipline is at the forefront of addressing the challenges posed by urban environments. Through rigorous testing, data analysis and a commitment to advancing autonomy across all levels of operation, Zipline is poised to significantly impact the drone delivery sector, offering a glimpse into the future of urban delivery services.
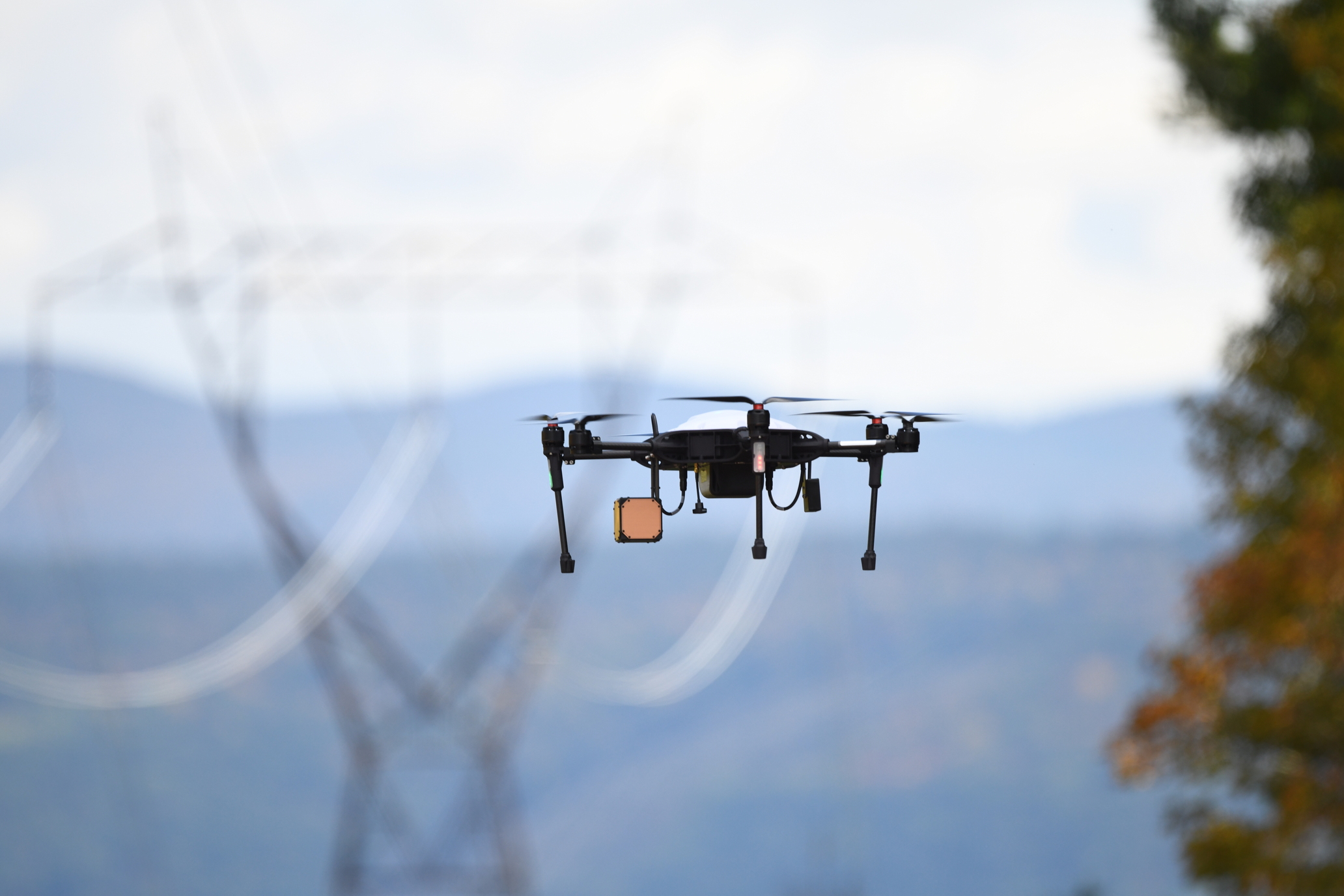
Leveraging Electromagnetic Fields for Transmission Line Inspections
In 2023 and 2024, the state of New York has experienced multiple severe weather events tied to climate change, causing widespread power outages impacting hundreds of thousands of families, individuals and businesses. The ability to quickly survey damages after a destructive storm, for example, will have a material impact on when repairs are made and power is restored. Targeting repairs to revive power systems after severe weather events, and perhaps more crucially to preventatively inspect effectively, requires specific field intelligence about transmission lines that are often in very difficult to access locations.
Though drones are well-established in infrastructure inspections, navigating around electric power transmission lines presents unique challenges, including visual estimation of distances, especially during flights along the transmission lines.
To overcome these hurdles, Manifold Robotics delivered an electromagnetic field (EMF) sensing solution to the New York Power Authority (NYPA). By detecting EMF emitted by transmission lines, the drones can identify the lines’ presence and estimate their proximity, autonomously avoiding collisions and tracking the line. Developing this technology required the creation of electric and magnetic field sensors with enhanced sensitivity, addressing size and weight limitations of small UAS.
“While strong EMF is often thought to be a nuisance for UAS, potentially interfering with sensors used to stabilize the aircraft, EMF emitted from transmission lines is fairly predictable and can be treated as a useful signal for navigation,” said Jeffery Laut, Manifold Robotics CEO.
Proprietary software algorithms analyze EMF data during flight, issuing commands for collision avoidance or autonomous line tracking. In shielded operations, also referred to as infrastructure masking, drones lock their location within a 100ft distance to critical infrastructure. The Manifold Robotics EM/Nav payload enables shielded operations using the transmission line EMF to set a drone’s position inside the shielded airspace.
“This technology does not rely on GPS waypoints for flying along transmission lines, but instead directly estimates its distance from the line,” Jeffrey Laut said. “This approach is expected to provide a compelling advantage for beyond visual line of sight flight along transmission lines for inspection purposes as it enables UAS to safely fly in close proximity to the lines where the risk of encountering other aircraft is insignificant—a concept known as obstruction shielding.”
More than 100 test flights were conducted using NYPA’s transmission line infrastructure. The system was effectively deployed tracking along a one-mile stretch of a 345-kV transmission line. The EMF sensing guided the UAS to maintain a safe 20-foot distance while flying parallel to the line, autonomously adjusting altitude to accommodate height variations due to line sag and terrain changes.
Doreen M. Harris, president and CEO of the New York State Energy Research and Development Authority (NYSERDA) emphasized in a press statement the importance of this technology for “evaluating infrastructure and enhancing the reliability of transmission lines amid the transition to a zero-emission electricity system.” Manifold Robotics recently obtained a BVLOS waiver from the FAA, based on the EMF technology’s success. This waiver allows UAS to cover far greater distances along NYPA’s transmission lines.
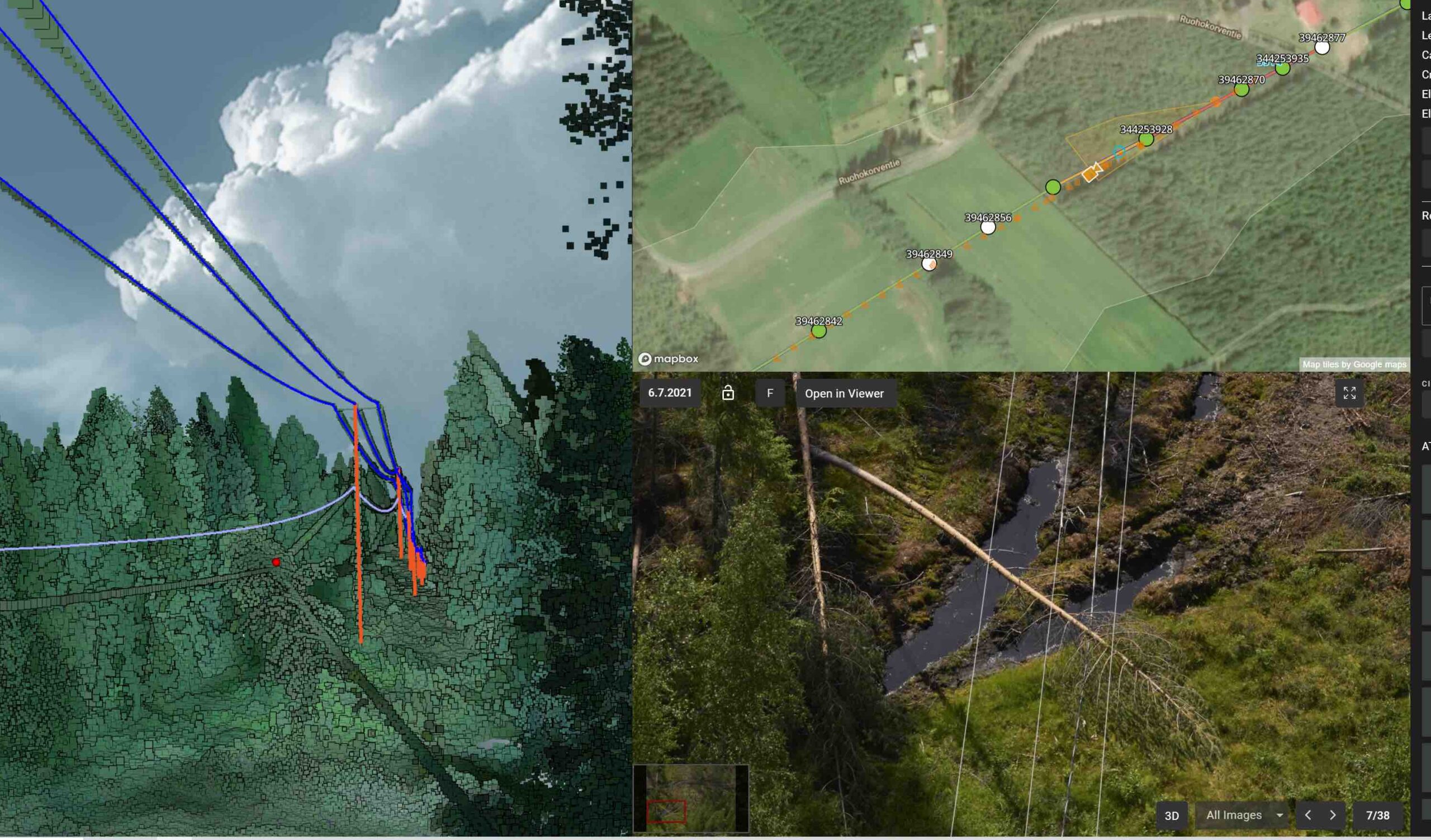
Digital Twins for Infrastructure Management
Another approach to power line inspection is based on a digital twin of the physical assets. Sharper Shape is a software platform designed to enhance utility asset management and inspection processes. At the core of Sharper Shape’s platform are three components: asset management, vegetation management and comprehensive reporting. Algorithms facilitate defect detection from images, analyzing vegetation’s growth on or near utility lines and identifying the tree species present. The platform forecasts future vegetation growth, enabling proactive management. Lisa Stannis, director of customer engagement at Sharper Shape, explained, “Once we create the digital twin…you have a digital replica at that moment in time of what your network looks like.” This digital twin becomes instrumental in post-catastrophic weather damage assessments, allowing for the rapid overlay of new data onto the existing digital model. Such capabilities enhance operational readiness and resilience.
The predictive analytics capability of a digital twin stands out as one of its most valuable features. By analyzing data patterns through AI and machine learning, the twin can forecast potential failures, suggesting preventive or corrective actions. This enables utility companies to proactively address issues, minimizing downtime and extending the lifespan of their assets. The twin acts as a decision-support tool, simulating various scenarios to understand the potential impacts, yielding insights to drive improved operations and planning.
Sharper Shape envisions its platform as part of the broader digital transformation impacting the utility sector. This transformation is marked by the shift from manual, in-field operations to technology-driven approaches that leverage drones, autonomy and AI to manage tasks like vegetation and powerline management.
Stannis highlighted industry trends toward decreasing numbers of workers qualified in electrical tasks and an ageing workforce. Stannis suggested that rapid digitization can transform legacy tasks and attract a new generation of workers interested in technology.
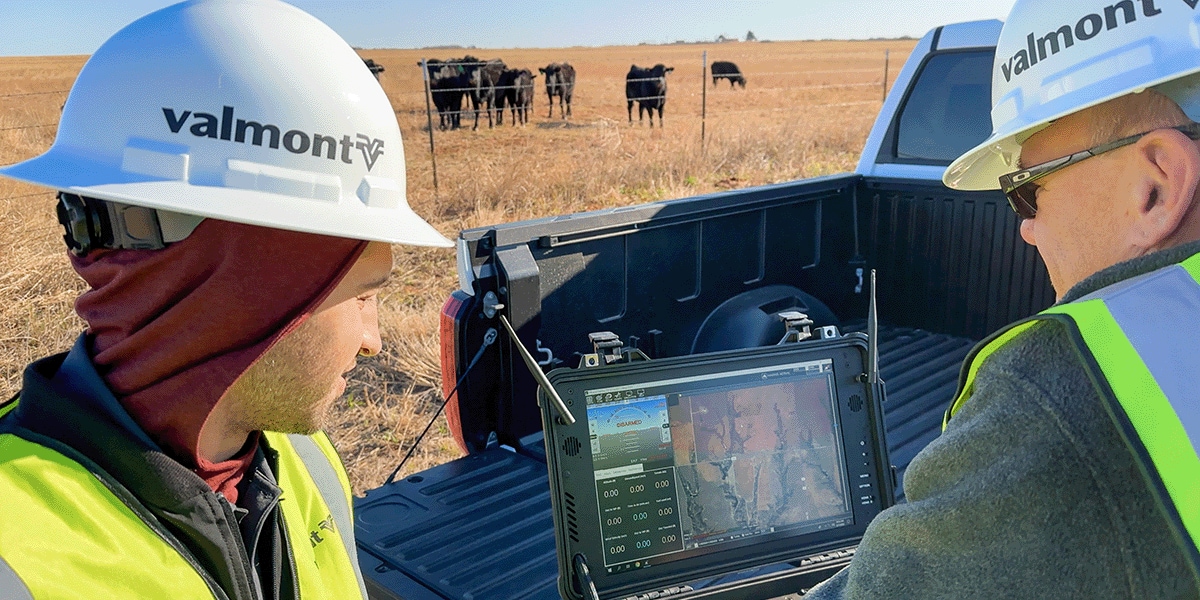
Autonomy’s Efficiencies for Clean Energy Operations
Autonomous drone platforms are also impacting the solar sector of the energy industry. Discussing Raptor Maps’ offerings, which encompass an autonomous drone-in-the-box solution as well as software and cloud-based data analytics, Leo Kim, director of marketing and growth explained: “At the core of Raptor Maps is AI, because AI not only enables the robotics to navigate and operate on site, but it’s also the backbone of our analytics. When the drone captures data, there’s not really a neat way you can stitch together all that information and localize that specifically on the solar farm [without AI].”
For AI and robotics to be applied on solar sites effectively, you need an operational blueprint of the site and its assets. Enter the digital twin, which provides, “an operational blueprint for the robotics unit to operate on site, for us to ingest the data and for us to analyze and return the insights to the user so that it’s done in an intuitive way. And it becomes a really comprehensive history of the asset,” Kim said.
Kim emphasized that the overall integration of the robotics, sensors, software and analytics are required to deliver the most operational efficiency. “You can collect data, and you can set up a dock or a drone-in-a-box on your site,” but you will not reap the maximum benefits “if you don’t have the software components to actually orchestrate and operate the dock autonomously and remotely…to ingest that data, and the analytics engine to interpret that data and return it for you as a user to consume the information in an actionable way.”
This approach to data analysis and interpretation—where every captured image, temperature variance, and identified anomaly is contextualized within a comprehensive platform—reframes how solar companies monitor and maintain their installations. The autonomy offered by Raptor Maps’ technology not only enhances operations and cost-effectiveness but also significantly improves safety. The drone-in-a-box acts as a first responder in potentially hazardous situations, mitigating the risk to human personnel by providing an initial assessment from a safe distance.
Kim explained, “No drone pilots means the marginal cost of data capture becomes near zero. You enable more frequent missions with high quality and consistent data capture.” An example is “if inverter performance is down in this block, you can send a technician to investigate. Or you can launch a mission for your drone-in-a-box on site and have it fly, collect data, and then our analytics engine will process that and report that this inverter block has this many issues, look at these modules.”
Kim continued, “A reason why I love drone-in-a-box so much is because it actually unlocks a really wide variety of use cases that were previously not that cost effective. An example would be monitoring the progress of your solar farm construction by sending a pilot to go out and fly the site. But then you have to find someone to go out regularly. And that costs you a lot. Second, the other alternative is to have someone count the modules on site. That is incredibly time intensive. So having a drone-in-a-box on site that allows for more frequent data collection…that becomes far more cost effective.”
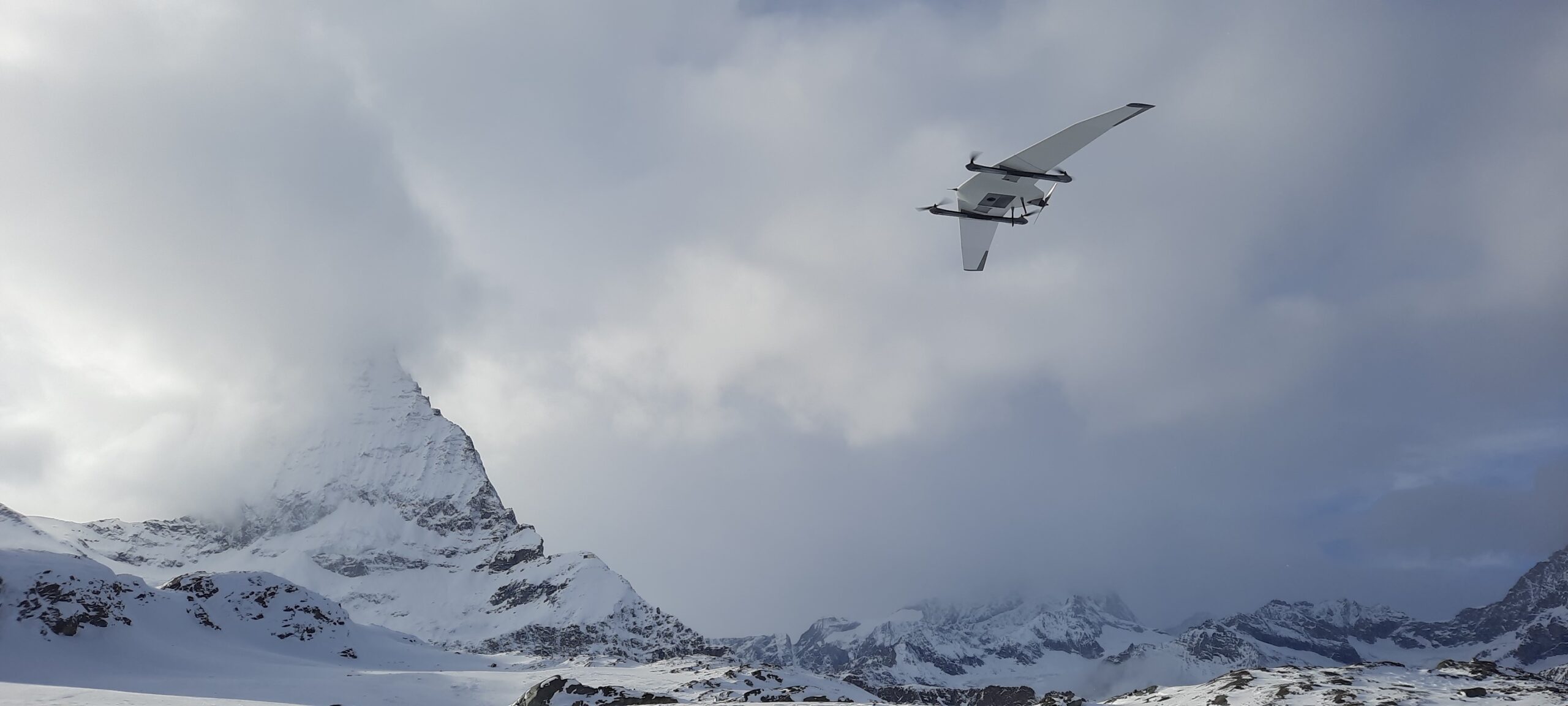
Instant Inspections for Commercial and Industrial Solar Sites
A growth area in clean energy is commercial and industrial (C&I) solar. It involves directly harnessing solar energy to provide power to facilities like shopping centers, offices and factories. C&I solar supports sustainability objectives and the installations are tailored to each facility’s energy requirements, including energy storage to enhance independence and reliability.
To support C&I solar operations, Raptor Maps has developed a new AI product called Instant Inspections. Kim explained it is geared toward “Rooftop solar on a Target or a Wal-Mart, for example. A technician who’s going on a regular maintenance visit can bring a drone, fly it, upload the data to Raptor Maps, and then while they are going through their checklist of regular maintenance activities, Raptor Maps’ platform processes and then delivers the analytics within 90 minutes, while they’re on site.” This allows for any issues identified in the data capture to be addressed right away, and significantly enhances the value of routine inspection procedures.
“We really believe that our technology, whether that’s robotics or AI, should empower every single person at the solar company. So, we’re not building for just the people in the office, we’re also building for the people in the field because they’re the ones fixing and addressing these issues.”
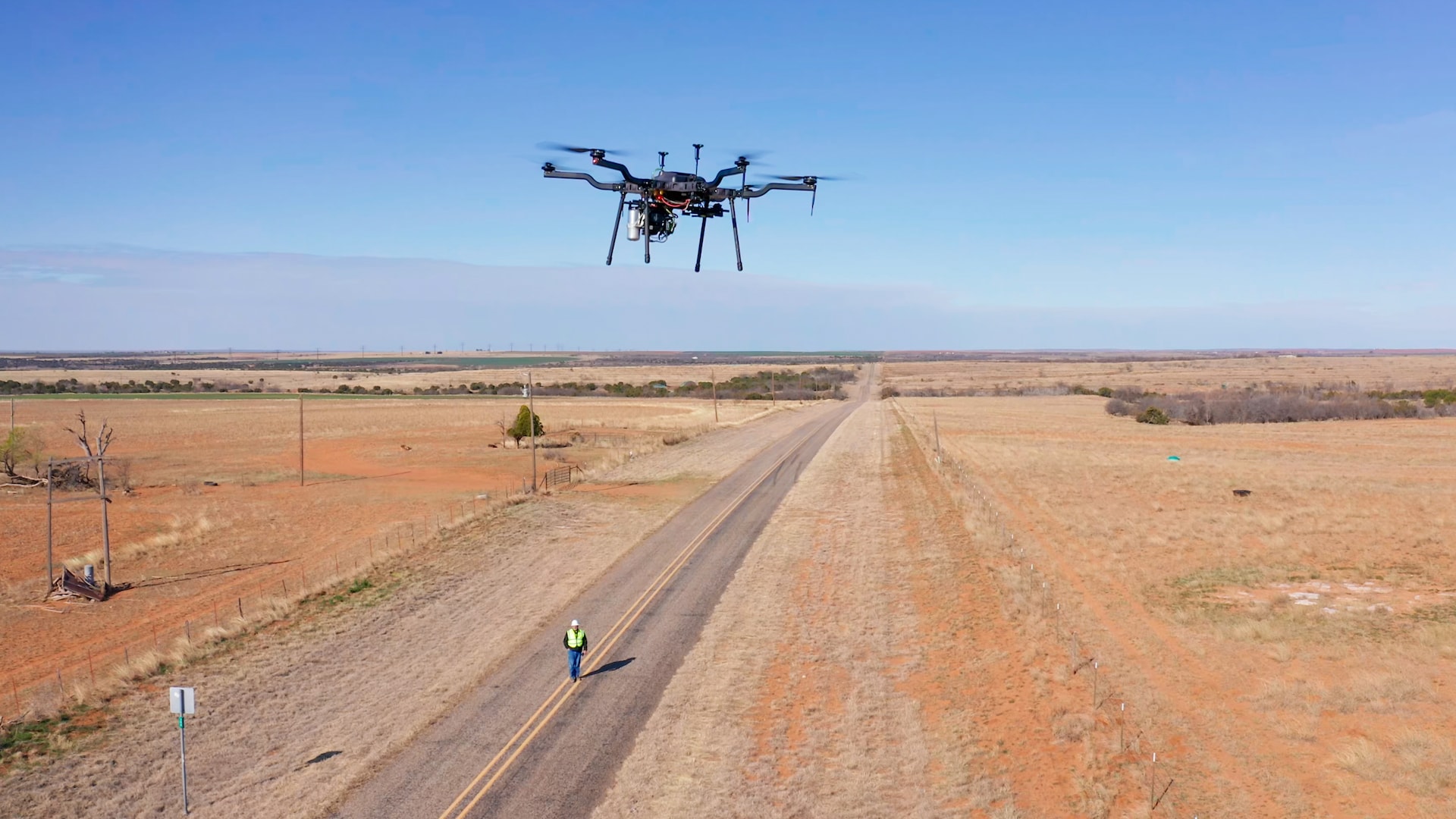
Extending the Distance of BVLOS Flights
A 2023 collaboration by Valmont Industries Inc., T-Mobile and Harris Aerial saw the successful completion of a 77-mile unmanned flight beyond visual line of sight, using the advanced capabilities of 5G technology. Valmont reported in March 2024 an even longer, 183-mile, single-day survey flight.
Using the Harris Aerial H6E drone equipped with a Sony A7RM5 camera payload connected to T-Mobile’s 5G network, the flight went from Childress, Texas to Aspermont, Texas. The drone’s journey involved the inspection of critical infrastructure components, including power lines, railroads and bridges, demonstrating the drone’s capability to capture high-fidelity data over long distances.
The integration with T-Mobile’s 5G network provided real-time data transmission and operational command over the drone, even in the rural expanses of this flight path. Continuous connectivity lays the foundation for real-time analysis and decision-making in a BVLOS flight. The long-range BVLOS drone operation completed the task three times faster than traditional methods. This efficiency not only translates to operational cost savings but also a reduction to the environmental impact compared to conventional inspection methods. Such methods have a much larger environmental footprint, involving human-piloted aircraft and extensive ground teams.
The viability of long-range BVLOS flights is predicated on regulatory advancements, with Valmont obtaining a waiver in this case from the FAA for BVLOS operations. The FAA approval, coupled with the mission’s adherence to National Defense Authorization Act (NDAA) compliance standards, illustrates the vital importance for industry to effectively partner with regulators and authorities to deploy safely and legally. The Harris H6E is among the drone models on the Defense Intelligence Unit (DIU) Blue UAS approved manufacturers list (see the deep dive into the Blue UAS program on pg. 52 of this issue).
“Range has been a hurdle in the drone inspection space, until now,” said Jake Lahmann, UAS manager at Valmont Industries Inc., according to a press statement. “To be able to get this kind of range in a single drone flight is really going to revolutionize the way the industry approaches infrastructure inspections.”
FAA Approval for BVLOS Swarms in Agriculture
The FAA recently approved drone service provider and OEM Hylio to operate large drone swarms beyond visual line of sight. This landmark decision enables the control of up to three drones, each weighing more than 55 pounds, by a single pilot without the need for a visual observer. This development heralds a new era of efficiency and autonomy in agricultural operations, showcasing the potential of drone swarms to reimagine industry practices and introduce new business models.
Arthur Erickson, co-founder and CEO of Hylio, underscores the transformative impact of this FAA approval on agricultural autonomy: “Swarming drones over 55 pounds has long been the desperately sought Holy Grail in the agricultural industry.”
The implications of this approval extend well beyond immediate productivity gains. It introduces a new paradigm in agricultural operations, where autonomous drone swarms can mitigate labor shortages by performing tasks traditionally requiring significant human labor. Erickson highlighted the sophisticated technology underpinning this autonomy, including advanced radar systems, ATSB transponders, and computer vision capabilities, ensuring safe and efficient drone operations without direct human oversight.
Erickson discussed the broader potential of this technology to act as a catalyst for further advancements in autonomous systems. The agricultural sector’s relatively low-risk environment provides an ideal testing ground for refining sensitive avoidance systems essential for the safe operation of autonomous drones. This could provide a “Trojan horse” effect for broader adoption of drone swarms in various sectors if they are proven safe and effective in a controlled environment like agriculture.
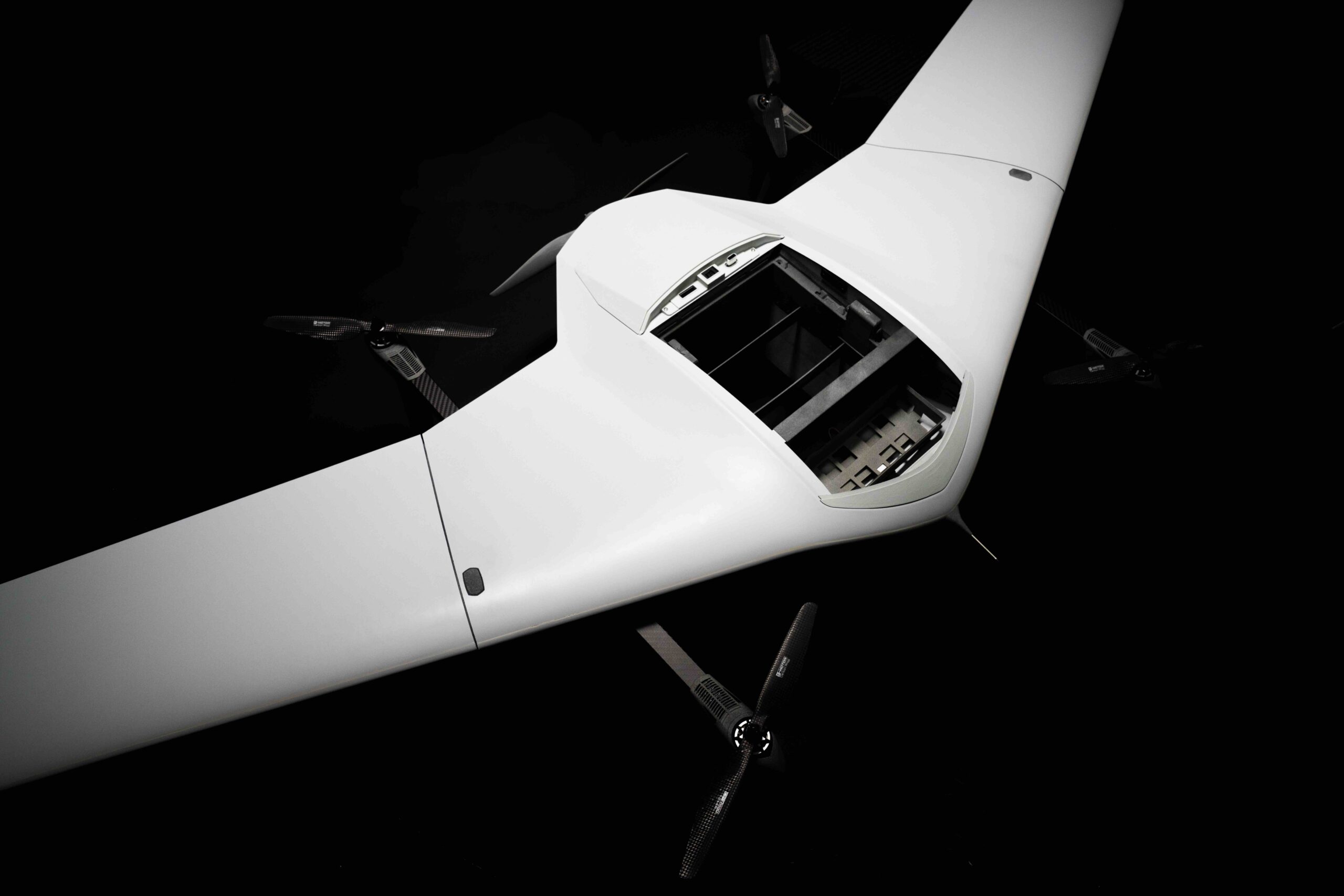
Security Applications and the Interconnected Tech Stack
Benji Pauly, solution specialist at Dutch drone manufacturer DeltaQuad, described how autonomous drones support security scenarios. “Minutes [matter for] military and police, and our flagship DeltaQuad Evo can fly for up to four and a half hours. You don’t know when the emergency is going to happen, you don’t know exactly what you’re looking for, or where exactly it is. So having that extra time means you can take off and be in the air without really having much insight into what you’re looking for.” DeltaQuad’s Evo UAS platform possesses a very high kilowatt hour per kilowatt, allowing up to 4.5 hours of flight time on an electric UAS.
With the drone capable of basing its next actions on contextual evidence discovered in-flight, security and defense teams “have the freedom to operate the Evo in a variety of different ways. For example, on the battlefield, they like to fly with a defined flight path, while other missions are more suitable for real-time control, and some require the convenience of automated tracking: the Evo adapts seamlessly to your needs,” Pauly explained. “And this information can be updated dynamically. The drone is just going to fly toward your point of interest. Our solutions and implementations are built for and proven in active war zones, which helps us save lives in practice, not just theory.”
This in-flight contextual evidence may indeed shift unpredictably as the scenario develops or change completely as the situation evolves. The autonomous capabilities of DeltaQuad’s Evo allow for flexibility in such situations. In GPS-denied environments, for example, you cannot depend on automated flight paths alone, as the satellite signals are often vulnerable to becoming a point of failure. The goal is to navigate increasingly congested and jammed EW (electronic warfare) environments without the need for pilot intervention over time and enable more autonomous capabilities.
“We take away as much responsibility from the pilot, as we aim for greater automation in navigation and safety. Eventually, we won’t even need pilots, the vehicles will be AI operated,” Pauly explained. “The Evo supports the MAVLink protocol, which is open source to guarantee interoperability with any supported payload or control system.”
DeltaQuad’s Evo becomes more effective through strategic partnership with software provider Auterion. The partnership introduces a layer of sophistication to the Evo VTOL UAS, enhancing its autonomous capabilities. This is critical in security scenarios where stealth and reliability cannot be compromised. Auterion’s advanced ISR features, including intelligent detection through onboard computing, computer vision processing, and AI, empower drones like the Evo to autonomously locate, identify and conduct continuous surveillance on objects of interest. These features align with Pauly’s vision of reduced pilot intervention, moving toward a future where drones fully leverage their autonomous capabilities.
In the dynamic landscape of autonomous drone platforms, the decision-making process regarding investments and operational objectives is pivotal. Pauly explained the fundamental question revolves around cost versus the intended application of the technology: “Currently, it’s a game of how much do you want to spend? And what do you want to do?”
Pauly’s insights extend into the broader strategy of balancing these choices: “So, it’s just the balance and the trade-off of what you want to do. And you recognize there’s not one solution that fits all [scenarios], but a combination of different approaches. And if you enable those combinations applied against [your problem set] and bring everything together into one ecosystem, you open a lot of doors.” The decision hinges on identifying the primary objectives of the drone’s deployment and aligning those with the capabilities of the platform.
Pauly suggested that embracing a combination of different approaches and integrating them into a unified ecosystem can unlock new possibilities. It’s about creating a system where the sum is greater than its parts, with each component contributing to a comprehensive solution that addresses the diverse needs of autonomous drone operations.
Where We Are and What Comes Next
The integration of autonomous drone technology into the operational fabric of essential industries optimizes existing workflows and unlocks potential for innovative business models and services previously not deemed feasible. This transformation is characterized by leveraging data sets for more insightful decision-making, activated by interconnected systems that streamline operations. Advancements in drone autonomy signal the evolution of the broader digital transformation that industries are continuously navigating.
These advancements indicate a future where the barriers between the digital and physical worlds blur, leading to a more integrated, responsive and intelligent operational ecosystem. Looking forward, the trajectory of drone autonomy promises to meet evolving challenges and create solutions that elevate business capabilities to better respond, adapt and thrive.