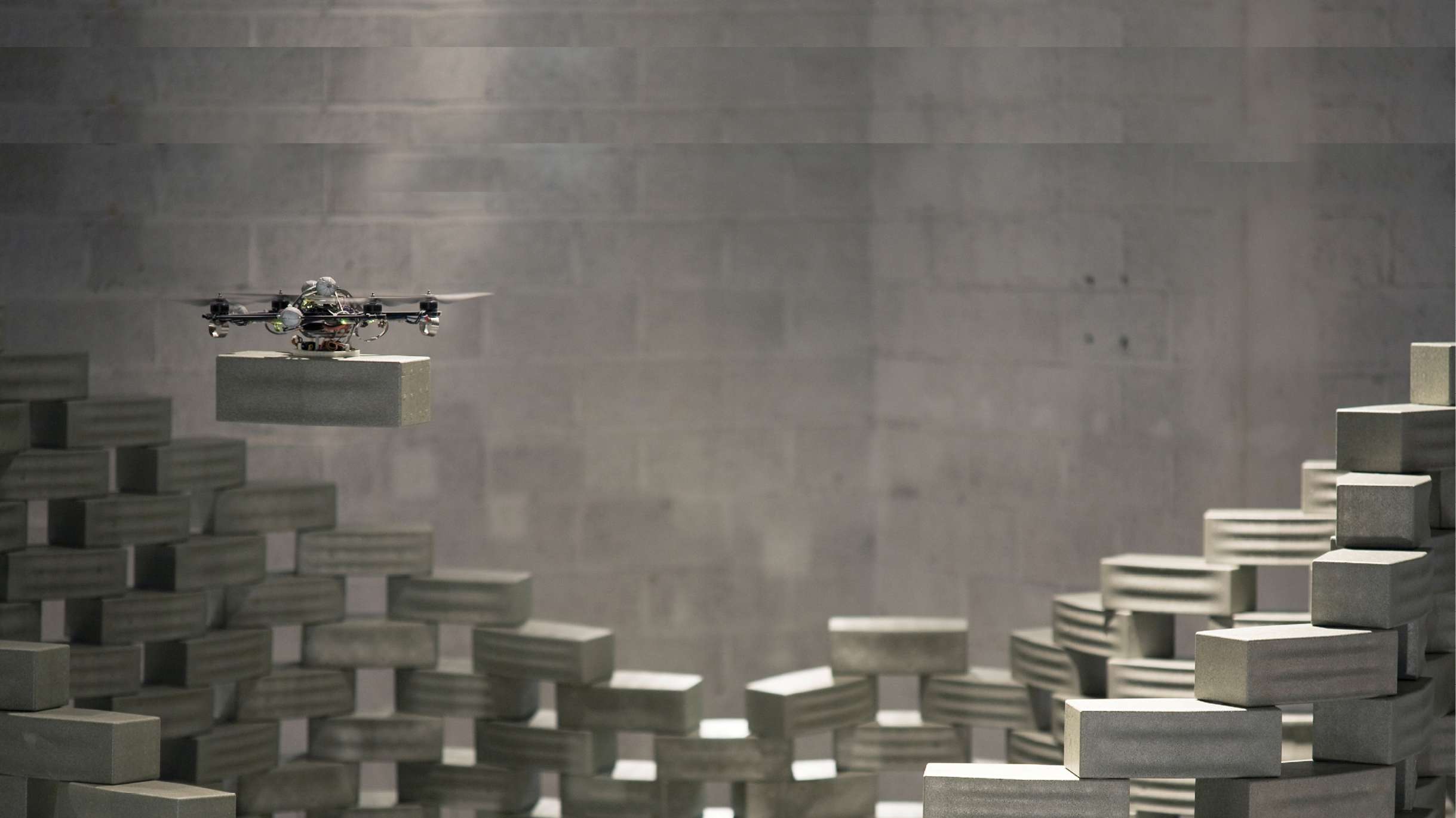
Photo courtesy of Gramazio Kohler architects
The $4 trillion construction industry is a complicated, big business fraught with danger.
Every project, from high-rise towers and business complexes to stadiums and transport systems, requires a tightly choreographed symphony of people, equipment and materials. On any given project, multiple tradespeople work side-by-side to erect steel, pour concrete, locate and place mechanical, electrical and plumbing systems, install windows, doors and walls amidst a vast array of equipment from cranes to power tools.
One misstep could cause injury or even death.
It would seem that robotic systems could provide an extra measure of safety, as well as a higher level of efficiency and machine-consistent quality. Yet, to date, the use of robotic systems on construction jobsites has been minimal.
John Voeller has been tracking the potential of robots in construction for 20 years. An ASME White House Fellow who has provided technical advice to Congressional policy makers and the White House Office of Science and Technology Policy, Voeller is a retired senior vice president and chief technology officer for Black & Veatch, one of the largest global engineering and construction firms in the world. He recalled for Inside Unmanned Systems how a large Japanese company spent millions in the early 1990s, pursuing different forms of robotics with limited results.
The building industry, however, is looking with fresh eyes at robots—including at least three new systems expected to be available this year—with a focus on near-term efficiencies that make investment in the systems make sense.
Demolition Days
Among the first fully-realized applications of robots in the construction environment are those used to support work that comes at the end of a structure’s life, namely demolition. In fact, remotely operated demolition robots have been around for more than a decade.
Large, international firms such as Brokk and Husqvarna produce commercially available remote-controlled robots for demolition. These robots are able to break down walls, crush concrete and even cut through rebar.
New classes of innovative demolition robots are also poised to enter the market. Researchers and established manufacturers are working to develop autonomous deconstruction robots that are able to scan, plan and sustainably erase a building without significant human intervention. Omer Haciomeroglu, a student at Sweden’s Umea Institute of Design recently designed a concept model for a highly energy efficient, robotic demolition system, called the ERO Concrete Recycling Robot. The ERO system would automate building demolition, as well as building material reclamation and waste disposal.
Dan Kara, the practice director for robotics at ABI Research, believes these remote-controlled demolition robots are the low-hanging fruit for the application of robotic systems and could inspire the use of such technology in other parts of construction.
“While these devices are not strictly robotic in that they cannot autonomously sense, think and then act, they are robotic in the broadest sense, much like aerial drones and mobile telepresencerobots. The articulated arms on demolition robots are very similar to those on industrial robots. Articulated arms can be fitted with end effectors that are designed for a specific task such as grabbing, cutting and smashing.”
But, can robots build?
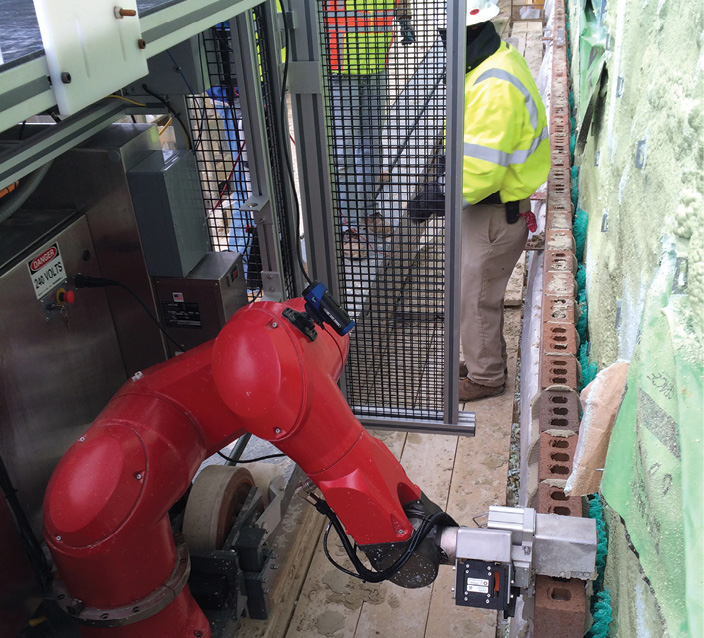
Bricklaying robot at work on the construction of a barracks at Fort Lee, VA Photo courtesy of Construction Robotics
Robotic Building Blocks
The short answer is, ‘Yes.’ There are robotic systems in development around the world that can lay bricks, set tile or finish concrete floors.
The Semi-Automated Masonry (SAM) system from Construction Robotics is a bricklaying robot designed to work alongside a mason. As SAM lifts and places the bricks, the mason focuses on site setup, tooling joints and finishing/quality control. SAM can lay roughly 230 bricks an hour and can handle brick sizes from modular to utility. In late 2014, a masonry contractor tested SAM on a barracks construction project at Fort Lee. The firm expects to produce a limited release of three SAM systems this year.
Similarly, the Future Cities Laboratory (FCL) of the Singapore-ETH Centre, in collaboration with its partner, ROB Technologies AG, is developing a robotic tiling machine. The robotic tiling machine prototype was tested by the Housing Development Board of Singapore at a public housing project construction site. A spokesperson for the Future Cities Laboratory believes the commercial version of the robotic tiling machine will be able to deliver an up to four-fold increase in productivity. A semi-autonomous robotic tiling machine is expected by the end of 2015.
Future Cities Laboratory is now collaborating on the second phase of the machine’s development with new industry partners SIKA Technology AG, a specialty chemicals company, and LCS Optiroc Ltd, a manufacturer of cementitious dry mortar products. The second phase is sponsored by global construction firm Bouygues Construction.
ROB Technologies has also developed FlexBrick, a robotic assembly process for non-standard brickwork, which is licensed to ROB’s industry partner Keller AG Ziegeleien, a company specializing in structural systems, façades, interiors and tunnels. The robotic assembly has been used to construct the façade for a winery in Fläsch, Switzerland, the façade for three residential blocks in Locarno, Switzerland, a wall for the new training stadium of Manchester City in England and acoustically active wall panels for a concert hall in Frankfurt, Germany.
ROB has also developed a second-generation, industry-applicable prefabrication system for masonry façades based on the bricklaying robot that will be able to handle every single brick differently.
“The robot will allow for the execution of complex and well detailed brick façades in a massive, homogenous appearance,” ROB Technologies’ Tobias Bonwetsch said. “The further optimization of the gluing system and the precision of the process enable the façade system to comply with existing building codes.”
Bionic Builders?
While not autonomous systems, robotic exoskeletons, those high-tech wearable suits seen in futuristic movies that help mere mortals defend Earth against other beings, could be a very real part of tomorrow’s jobsite and a possible precursor to autonomous robots in the field.
ABI Research’s Kara believes robotic exoskeletons could find use in jobs that require a lot of repetitive lifting, standing or squatting, but are unsuited for fixed automation solutions.
“Construction workers are already comfortable with battery-powered devices and tools,” Kara told Inside Unmanned Systems. “An exoskeleton is simply an intelligent, sensored extension of these existing tools.”
CYBERDYNE, a venture capital firm established by Yoshiyuki Sankai from the University of Tsukuba in Japan, developed the robot suit HAL (for Hybrid Assistive Limb), a new industry assistant-type exoskeletal robot. HAL is specifically designed to provide extra lifting power to workers. Obayashi Corporation, a major Japanese construction company, has been testing the new HAL exoskeleton on several construction sites since September 2014. HAL is expected to become commercially available in 2015.
Similarly, Lockheed Martin is developing a next-generation, unpowered, lightweight exoskeleton called FORTIS to enhance user strength and endurance. The FORTIS exoskeleton increases an operator’s strength and endurance by transferring the weight of heavy loads from the user’s body directly to the ground. Using various mechanical arms, operators can effortlessly hold heavy hand tools, increasing productivity by reducing muscle fatigue. The National Center for Manufacturing Sciences (NCMS) for the U.S. Navy has ordered two FORTIS exoskeletons to test and evaluate for industrial use.
“Advancements like FORTIS that use human vision and judgment, but multiply human effort, are the focus of many robotic research laboratories because the systems provide immediate results,” Voeller said. “Then, it’s a straightforward task to add better motors, sensors and batteries into future robots. A properly instrumented exoskeleton could also help gather knowledge about how construction workers perform tasks and the level of effort required. That information could then be used to teach an autonomous robot to perform the same work.”
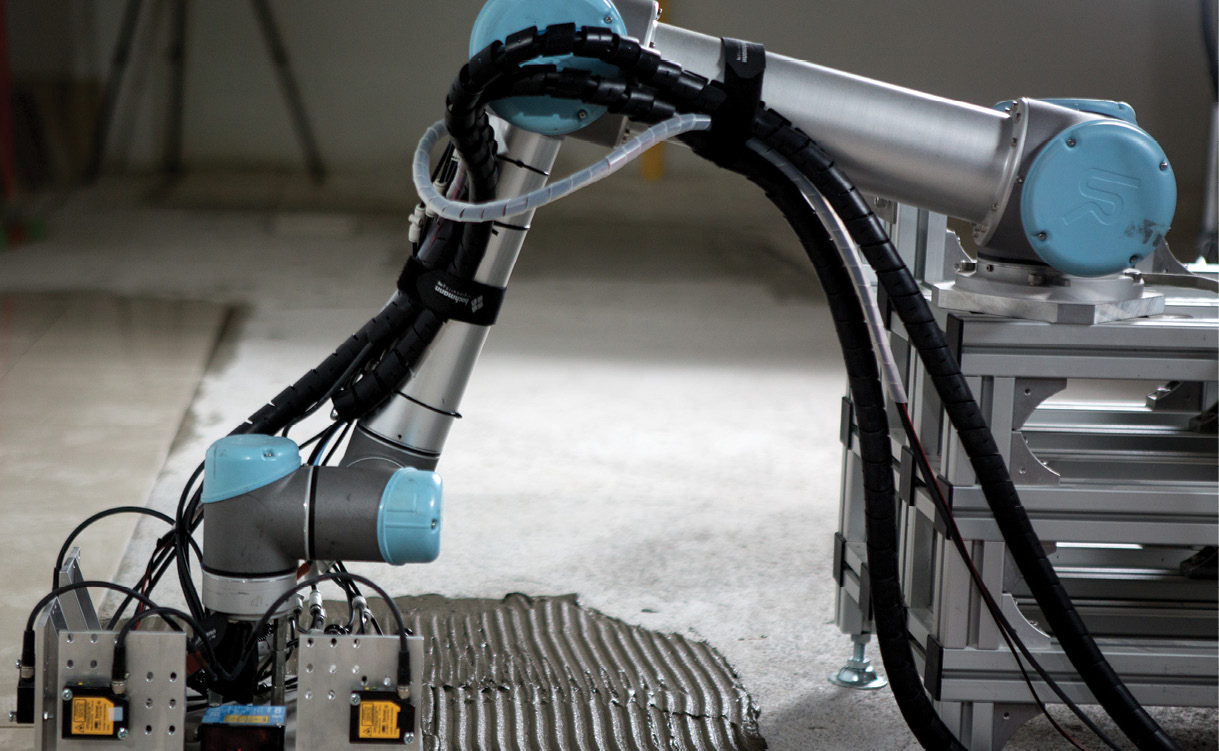
Robotic tilling machine recently prototyped at public housing project in Singapore.Photo courtesy of Future Cities Laboratory
In Search of Autonomy
Demolition robots, brick laying robots and wearable bionic suits have a place in the construction world and the ability to provide some return on investment. But, what about intelligent robotic systems that work alongside construction crews—autonomous systems that can sense, think and act on a jobsite?
While technology of this nature is still limited, recent research on a system inspired by termites suggests what might be possible. Computer scientists and engineers at the Harvard School of Engineering and Applied Sciences (SEAS) and the Wyss Institute for Biologically Inspired Engineering at Harvard University created an autonomous robotic construction crew called TERMES that could build complex structures without supervision. TERMES demonstrated that collective systems of robots can erect towers, castles and pyramids without the need for a central command or prescribed roles. While the four-year project was completed in 2014, similar robot systems could be used to lay sandbags in advance of a flood, or perform simple construction tasks on Mars, according to the Harvard researchers.
Both Voeller and Kara believe there is a place for robotic technology in the construction process and expect technology pioneers to continue to develop and adapt intelligent robotic solutions. In fact, Voeller is preparing an analysis for the FIATECH organization looking at the application of advanced artificial intelligence (AI) technology in construction. FIATECH (Fully Integrated and Automated Technologies for Construction), was formed in 2000 to promote development and adoption of innovative practices and technologies on capital projects.
Perhaps there’s a place in the industry for a robot like Sawyer from Rethink Robots. Sawyer is a high-performance collaborative robot developed for the manufacturing industry with AI capabilities. It has 7 degrees of freedom and a 1-meter reach. Each joint is embedded with high-resolution force sensing capability that the robot’s developers say allows it to “feel” its way into fixtures or machines, even when parts or positions vary. Sawyer also features an embedded vision system, which includes a camera in its ‘head’ to perform applications requiring a wide field of view and a Cognex camera with a built-in light source in its wrist for precision vision applications. Sawyer’s vision system may eventually enable the robot to read barcodes or recognize objects.
“There is a rich spectrum of opportunities for AI and robotics to enhance the construction of large capital projects,” Voeller told Inside Unmanned Systems. “However, setting the stage for these technologies will require a high level of integrated thinking to address the issues and a clear line of sight to solutions that can bring real value and withstand the rigors of the construction environment and the penalties of improperly managing risk.”
Kara believes construction companies charged with building very large, complex structures will adopt semi-autonomous and autonomous robotic systems in the near future if they can realize a return on investment in terms of increased productivity, safety and quality.
“This is already occurring in pockets throughout the construction industry,” he said. “I expect to see considerable growth in this market over the next 5 to 10 years.”