Robots that fly, swim and crawl through pipes are helping with the clean up of radioactive zones by mapping hard-to-find nuclear waste.
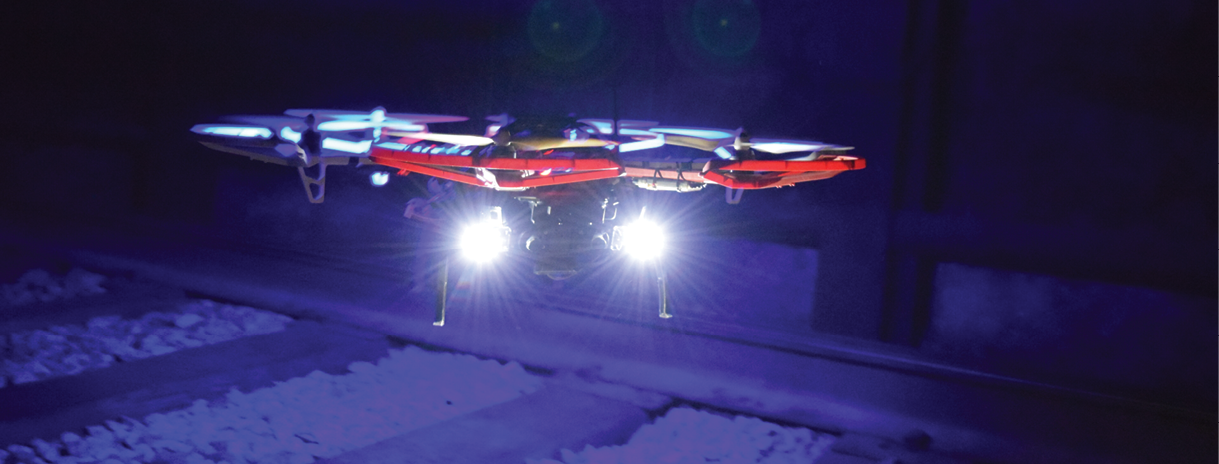
This prototype drone, built by the University of Nevada, can map nuclear waste storage tunnels.
To clean up nuclear waste at sites such as Fukushima, decontamination teams must first find out exactly where radioactive materials have accumulated. Now, researchers are developing robots that can fly, swim and even crawl through pipes to map out precisely where radioactive waste is hiding.
“Ideally, robots go where you don’t want to put a person, such as a radiation hazard,” said Kostas Alexis, an assistant professor of computer science and engineering and head of the Autonomous Robots Lab at the University of Nevada, Reno. “Also, robots can go where people don’t have easy entry, such as a sealed site—if you wanted to put a human in there, you’d have to open it, which can be quite costly, and then follow special procedures that may put humans at risk. A robot would be comparatively low in cost and greatly reduce risks.”
Robots also can be much more systematic and consistent in their inspections than people, Alexis said. “You can track changes in radiation levels at the centimeter level, and know what the changes are at every point on a map, which can help you infer the potential radiation hazard much better.”
What has limited the use of ground robots at nuclear waste sites is that sometimes they must traverse narrow spaces and terrain that is not flat—and there might be buildings on the sites with multiple stories, Alexis said. “Land rovers generally cannot deal with going from one floor to another.”
FLYING UNDERGROUND
Unmanned aircraft systems (UAS) can be used to map radiation in such hard-to-reach areas, Alexis said. “(The) ones flying above Fukushima were an excellent example of such technology. The difference with our system is that we’re flying mostly underground.”
Alexis and his colleagues experimented with a small UAS and successfully completed a proof of concept for a UAS that could autonomously fly itself through dark corridors looking for nuclear radiation.
“We’ve built a flying vehicle that simultaneously 3-D maps and radiation maps in dark, GPS-denied airspace,” Alexis said.
This new work is part of a National Robotics Initiative project designed to help clean up 107 legacy sites of the Manhattan Project around the country that have been shuttered for decades. The data these robots gather will help the U.S. Department of Energy develop a cleanup plan for all these contaminated sites.
For their experiments, the scientists built a hexarotor drone weighing just 2.6 kilograms (5.7 pounds). This prototype could fly autonomously with the aid of a Pixhawk autopilot module for attitude control and an Intel NUC5i7RYH mini PC computer to help it map its surroundings, control its position and plan its route.
The radiation detector the scientists used on the robot was based on a Scionix V10B10 miniature thallium-doped cesium iodide scintillator crystal combined with a silicon photomultiplier and a light sensor. When gamma rays from radioactive material strike the scintillator, it gives off light the silicon photomultiplier can amplify enough for the sensor to detect. All in all, the entire radiation sensor weighed just 41 grams.
“The scintillator is a consistent model we can trust in for years to come,” Alexis said, “and through spectroscopic analysis of the radiation, it can not only tell the intensity of the radiation, but the type of material that produced it, such as cobalt, cesium or uranium.”
The prototype was equipped with a stereo camera, as well as LEDs to help it see in the dark, with the LEDs synchronized to flash in time with the camera’s shutter for the most efficient use of light. ROVIO (Robust Visual Inertial Odometry) software used data from the camera and an inertial measurement unit (IMU) to help perform odometry. Depth perception was achieved using either the stereo camera or LiDAR.
“As we were carrying out this research, we had synergy with other projects we had involving exploring mines and other subterranean environments with drones, where dust or smoke can potentially degrade their vision,” Alexis said. “The more degraded their vision becomes, the more we factor in uncertainty into collision avoidance. Another way we’re dealing with dust or smoke is to work with thermal sensors that can help the drone see past such obstacles.”
Alexis and his colleagues tested their prototype in both a lab and a train tunnel in Nevada. They placed radioactive samples of cesium-137 in both sites as the robot flew around. Their UAS built 3-D maps of the environments, erring on the location of the radiation sources by about 25 centimeters, “which is still reasonably accurate enough,” Alexis said.
One challenge in working in underground environments “is that everything can look more or less the same,” Alexis said. In such parameter-less environments, there are not that many details for the mapping software to use to indicate location. By working with multiple sensors, “the aim is to give the software something it can track,” he noted.
Alexis and his colleagues have moved from their prototype radiation-mapping drone to a modified DJI Matrix 100. While the initial prototype had to stop regularly to take radiation measurements, “we can now measure on the fly,” Alexis noted.
The researchers aim to use aerial robots to map Plutonium-Uranium Extraction (PUREX) tunnels, where multiple train cars hold nuclear waste.
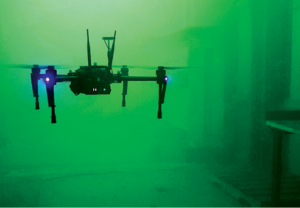
SEEING IN THE DARK
The University of Reno prototype used stereo cameras, LEDs and an inertial measurement unit (IMU) to help it navigate underground.
“Our final goal is a system of systems, where multiple robots can access underground environments, map them, and annotate these maps with radiation measurements,” Alexis said. “We want multiple-robot capabilities because as long as we deploy single robots, we’re sensitive to single points of failure. However, working with multiple robots presents two challenges—how to coordinate and plan their activity, and how to share their knowledge so they know not to just map the same spots.”
Aerial robots are also being used at Sellafield in England, the birthplace of Britain’s nuclear industry, Europe’s largest nuclear site and the site of its worst nuclear accident. One of Sellafield’s reactors caught on fire in 1957, contaminating the surrounding farmland. Hundreds of tons of radioactive material remain at the site.
The RISER (Remote Intelligent Survey Equipment for Radiation) is the product of a collaboration between England-based firms Createc in Cockermouth and Blue Bear Systems Research in Bedford. It’s a quadcopter that can navigate inside a building without GPS, and is equipped with radiation sensors that enable it to build up 3-D radiation maps. The drone was designed to explore the inside of a tall chimney at Sellafield that was built to ventilate the original reactors there, and which was heavily contaminated during the 1957 fire when radioactive plumes from the burning reactor core spewed out of it.
RISER already has been successfully tested inside the chimney and will find use elsewhere at Sellafield as well. “What’s exciting about all this work is how useful to society it is,” Alexis said.
PIPE CRAWLERS
Before obsolete nuclear fuel sites can be decommissioned and dismantled, contractors first need to inspect miles upon miles of pipe. “We need to understand the amount of uranium there may be in a pipe to remove it and dispose of it safely,” said Rodrigo Rimando, director of technology development for the U.S. Department of Energy’s Office of Environmental Management.
The nuclear industry depends on uranium. The element mainly comes in two isotopes—uranium-238, which makes up about 99.27 percent of natural uranium, and uranium-235, which makes up roughly 0.72 percent. (All isotopes of an element have the same number of protons, but each has a different number of neutrons—for instance, uranium-235 has 143 neutrons, while uranium-238 has 146.)
The kind of nuclear chain reactions that both nuclear reactors and nuclear weapons depend on are possible with uranium-235 but not with uranium-238. During the Cold War, uranium enrichment plants often forced a gas of uranium-laden molecules through membranes that could separate the lighter uranium-235 from the heavier uranium-238, resulting in “enriched” uranium with high concentrations of uranium-235. This process typically left deposits of radioactive waste clinging to the insides of miles of the plants’ “process pipes.”
“These deposits almost look like a thin layer of paint inside the piping,” said William “Red” Whittaker, a robotics professor and director of the Field Robotics Center at Carnegie Mellon University in Pittsburgh. “This material is deposited during a chemical reaction with the uranium-laden gas with water or something else that would provide oxygen.”
Whittaker and his colleagues have now built an autonomous robot called RadPiper to help detect this hazardous nuclear waste at the Department of Energy’s 3,778-acre Portsmouth Gaseous Diffusion Enrichment Facility in Piketon, Ohio. Shuttered since 2000, this plant began operations in 1954, and with 10.6 million square feet of floor space, it was the Department of Energy’s largest roofed facility. Three large buildings contain enrichment process equipment that spans an areas the size of 158 football fields and contains more than 75 miles of process pipe.
Locating the nuclear waste throughout the huge facility is a herculean but essential task before the Department of Energy can decontaminate, decommission and demolish it. In the Portsmouth plant’s first process building alone, human crews performed more than 1.4 million measurements of processing piping and components manually over the past three years before they could declare the building “cold and dark.” The next process building has more than 15 miles of piping that needs scanning, which robots could help with immensely, Rimando said.
Scientists at Carnegie Mellon University were paid $1.4 million to build RadPiper as part of what the university calls the Pipe Crawling Activity Measurement System. The researchers developed the robot in close collaboration with Fluor-BWXT Portsmouth, the contractor that the federal government hired to decommission the Portsmouth facility.
Whittaker has a great deal of experience with robots in nuclear facilities, including the design and construction of robots that helped gather data and remove debris after the partial meltdown at the Three Mile Island reactor building in Pennsylvania in 1979. He and his colleagues also developed robots to help with inspections in the aftermath of the Chernobyl disaster in Ukraine in 1986.
The conventional technique for identifying hidden deposits in process pipes involves people with handheld radiation detectors scanning process pipes from the outside in search of the gamma rays from radioactive isotopes. However, “since you’re measuring from the outside, those gamma rays can be attenuated by the pipes themselves,” Rimando said.
This method is time-consuming and labor-intensive. “You have to hold the detector outside the pipe for at least 30 seconds before you move a foot or so further down to measure the next segment,” Rimando said. “And many of these pipes are overhead, and normally need a scissor lift or some other platform to access, and as you move down a pipe, you’ll need to move the scissor lift to a new location as well. Logistically, there may also be issues getting a lift in certain places in a building, and the stanchions and brackets holding up the pipes can be very difficult to maneuver around as well.”
In addition, “the workers have to wear suits with visors and closed breathing systems,” Whittaker said. “Until you’ve operated in those things, it’s hard to describe the challenges with visibility and manipulation with gloves you face, and depending on the weather conditions, how hot and confining they are.”
Instead, RadPiper will find these radioactive deposits by traveling inside the pipes. “By taking measurements directly inside the pipe, all these considerations regarding attenuation are not an issue,” Rimando said. “And RadPiper can scan as it moves continuously without stopping. The reason people have to stop when scanning from the outside is because they have to wait for measurements to come in since a pipe can weaken signals traveling through it, but by scanning within the pipe, RadPiper avoids that concern. It is much more efficient.”
RadPiper is a tetherless robot designed to move on a pair of flexible tracks like a miniature tank or bulldozer. “Going tetherless gives the robot a lot of freedom to operate,” Rimando said.
Tethered robots have a decades-long history of use in nuclear facilities. Tethers can offer virtually unlimited power as well as wires for communications. And a tether can serve as a leash to help winch a robot back if necessary.
However, “in the types of environments we are sending robots, one concern is that the tether can be severed or even simply disconnected, and then that’s a real pickle—you’ll lose communications, you’ll lose control and you’ll lose your recovery capabilities,” Rimando said. “Also, in areas with radioactive contamination, the tethers can disturb those contaminants and spread them, and when you’re dealing with fissile materials, you don’t want that material to accumulate and raise concerns it might go critical. Advances in robotics, batteries, wireless communications and microprocessors now help give tetherless systems a lot of capabilities.”
RadPiper is about 45 inches long by 17 inches wide and 21 inches tall, and weighs approximately 180 lbs. Sensors in its tracks help measure the distance it has traveled, and an inertial measurement unit (IMU) and laser rangefinder help the robot stay upright and keep track of its position.
RadPiper is equipped with a fanless embedded Intel quad-core i7 system as its main computer. The robot is equipped with two LiDAR rangefinders, a fisheye camera, eight white ultraviolet LEDs to help it see obstructions such as closed valves, and eight ultraviolet LEDs that can make uranium-loaded deposits visibly fluoresce. After scanning a stretch of pipe, RadPiper automatically returns to its launch point.
The robot’s Canberra Osprey radiation detector uses a standard sodium iodide sensor to count gamma rays. The sensor is positioned between two large lead disks that block gamma rays from radioactive deposits that may lie beyond the one-foot section of pipe the sensor is scanning at any given time. “These lead disks let you know what exactly the robot measured from a given slice of the pipe, without having to worry about interference from elsewhere in the pipe,” Whittaker said.
A USB data drive is used to store data from each run and transfer it to a computer. Analyzing the data is an automated process that takes a few minutes on a laptop, and the results include a chart of deposits plotted with respect to distance inside the pipe, as well as visual imagery.
A pair of lithium iron magnesium phosphate battery modules can help the robot operate for five hours and a maximum total round trip of 600 feet. Battery charging time is typically two hours, allowing for rapid turnaround.
To help prevent nuclear waste from clinging onto RadPiper, the robot’s contours are as round as possible, Rimando said. After RadPiper emerges from a pipe, researchers wipe off any contamination on the robot.
RadPiper is designed to move through horizontal pipes with only minimal inclines. “Vertical pipes would demand a whole separate design, and honestly, there are not that many vertical pipes in these plants,” Rimando said. “When you are enriching uranium, you want gas containing it to flow as straight as possible. You want to be very careful to not create instances where you would interrupt that flow, since you do not want it settling down and potentially depositing uranium-235 within the pipes—you want to recover as much uranium-235 from the gas as possible.”
For 30-inch pipes, RadPiper can scan at speeds of more than 30 feet per minute. “Our initial estimate for the amount of time RadPiper can save is that for every eight hours of conducting surveys with handheld equipment, RadPiper can do it in an hour, and that eight-to-one ratio is likely an underestimate,” Rimando said. “Moreover, the data quality is much, much better because it is taking direct measurements instead of through a pipe—the error band is reduced by 50 percent, if not more. That is a huge improvement.”
In addition to saving time and labor, RadPiper promises to significantly reduce hazards to workers who would otherwise have to perform radiation measurements by hand. “We are not sure yet how much fewer people are needed with RadPiper—we will know much better when we have more runs with it under the belt,” Rimando said.
The scientists tested the RadPiper prototype in late 2017 at the Portsmouth facility. The robot successfully traversed pipe and measured radioactive deposits to a resolution, accuracy and speed unachievable by alternate methods.
Live hot tests with the final design of RadPiper were underway in July, Rimando said. The robot will be delivered to Fluor-BWXT Portsmouth to work at the Portsmouth facility in August or early September, he added.
The pipe segments that RadPiper detects as having hazardous deposits will be removed and decontaminated. The vast majority of the Portsmouth facility’s piping will remain in place and be demolished safely along with the rest of the facility.
Researchers estimated RadPiper “may save anywhere from $10 million to $50 million per facility,” Rimando said. “Once RadPiper is deployed, the real number-crunching will begin. It might end up saving hundreds of millions of dollars per plant.” They suggested RadPiper could find use at the uranium enrichment plant in Paducah, Kentucky, as well as elsewhere in the Department of Energy’s defense nuclear cleanup program, which is not even half complete, Rimando said.
RadPiper is designed to initially operate in pipes measuring 30 inches and 42 inches in diameter. “We are now interested in designing a system for pipes 10 inches in diameter,” Rimando said.
DIVING INTO FUKUSHIMA
Robot submarines are at work at nuclear sites as well. In fact, in 2017, one finally found the melted uranium fuel rods at Fukushima.
The 2011 earthquake and tsunami in Japan triggered meltdowns at three of the six reactors at the Fukushima Daiichi Nuclear Power Plant. For years, no one could find the hundreds of tons of fuel inside these reactors that overheated, melted and burned through their steel containers. This made it virtually impossible to design a plan to get rid of this nuclear waste.
Humans naturally could not enter these lethally radioactive reactors, so efforts to look for this missing fuel relied on robots. However, for years, robots had failed in this mission—blocked by debris or disabled by radiation that ruined their electronics.
In 2017, researchers finally discovered the fuel using a submersible robot created by Toshiba Corporation and Japan’s International Research Institute for Nuclear Decommissioning. Named the Mini-Manbo, or “little sunfish,” the underwater remotely operated vehicle (ROV) was roughly 13 centimeters wide, 30 centimeters long and 2 kilograms in weight, with electronics hardened against up to 200 sieverts of radiation. (A dose of one sievert is enough to cause radiation sickness in a human.)
The robot used five tiny propellers to hover and glide through the water pumped into the Fukushima’s Unit 3 reactor building to cool it down after the disaster. The ROV was just small enough to fit through the roughly 5.5-inch hole leading into the unit’s primary containment vessel.
Equipped with front- and rear-facing cameras and LED lights, the robot delivered a video feed to its operators. Powered and remotely controlled via wire, it took three days for the robot’s operators to navigate it through the Unit 3 reactor building to the reactor itself. There, it transmitted video of a hole at the bottom of the reactor, and the melted uranium fuel on the floor beneath it. The researchers later had similar successes at Fukushima’s other two ruined reactors.
Japan is now “developing systems like RadPiper to enter internal spaces like piping,” Rimando said. “Our work with RadPiper could help support later decontamination efforts at Fukushima.”