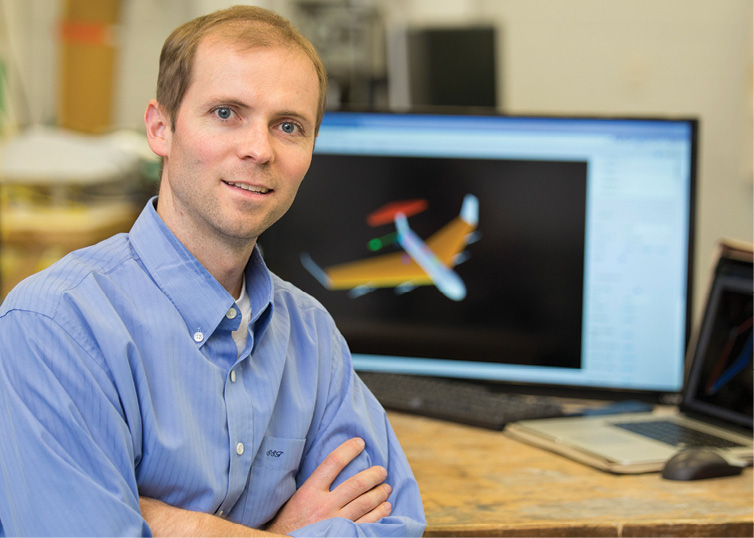
Doug Hunsaker
Drone startup companies raised more than $450 million in venture capital across 74 deals in 2015, according to CB Insights of New York, which tracks new drone firms and venture capital, a sign of how big a role drones may soon play in everyday life. Now a free online 3-D aircraft design software package is available to help drone startups and university researchers design unmanned aircraft to support this revolution.
Like the Internet and GPS before them, drones have evolved beyond military applications to become powerful business tools. In a March 2016 report, Goldman Sachs estimated that total global spending on unmanned aircraft in the commercial market will reach $100 billion in the next five years, with firms increasingly providing hardware, flight and data services to the construction, agriculture, energy, utilities and mining industries as well as emergency responders, real estate agents, insurance companies and media firms.
Engineers are working furiously to create new platforms able to fly even more economically, operate in difficult environments and enable new applications like asset tracking. Now a free online 3-D aircraft design software package is helping drone startup companies and university researchers design unmanned fixed-wing—and soon rotorcraft—aircraft to support this revolution.
“There are thousands of different missions people are coming up with for drones,” said Doug Hunsaker, an assistant professor of mechanical and aerospace engineering at Utah State University. Before his current academic position, Hunsaker was a design engineer for Scaled Composites, the California company behind Virgin Galactic’s SpaceShipTwo suborbital spaceplane. He was also co-founder and CEO of Utah-based Blucraft, which provided web-based computational tools to the aerospace industry designed for quickly analyzing and optimizing airframe designs.
Designing any aircraft involves knowing its mission, what payload it needs to carry at what altitude, the speed the payload travels and the time you want it to stay in the air. For example, “a pipeline surveillance drone might have thousands of miles of pipeline that it wants to inspect,” Hunsaker said. “It might have a few cameras, infrared or color, or a sniffer for gases coming out of the pipeline—and you’d want it to have endurance.”
In contrast, “for a search and rescue airframe here in the Rocky Mountains, where people get lost hunting or rock-climbing, you maybe wouldn’t want as much endurance, but it needs to be faster and more agile to get in and out of canyons and mountain valleys easier,” Hunsaker said. “And Amazon’s delivery drone has to be able to stop and hover.”
Free Online Design Software
Nowadays designing any aircraft, including drones, calls for sophisticated computer tools. This is where MachUp comes in. Users do not have to download any software—this web-based 3-D aircraft design tool works on any browser and on any platform, including smartphones and tablets. MachUp is available to anyone at http://aero.go.usu.edu.
“I wanted to give people an opportunity to design airframes and analyze them and not have to have a PhD to do it,” Hunsaker said. “A lot of the aircraft design software out right now requires a big learning curve. I tried to make the code smart enough to do things without needing the user to know how to do those things.”
MachUp lets users design an aircraft, including wings, propellers and basic shapes, and uses 3-D web graphics to render images in a browser. The site also features training tutorials and how-to videos.
“You can very easily sketch up an airframe,” Hunsaker said. “A lot of startup companies in the drone industry constantly do napkin sketches. It almost takes more time to draw on paper than to put it on MachUp. The quickness with which you can sketch on MachUp is really valuable for drone startup companies, which are constantly iterating, looking at different configurations.”
Software on a dedicated MachUp server will calculate aerodynamic information about the geometry of that airframe, such as lift, drag and stability. “All the heavy lifting is on our end,” Hunsaker said.
“I did this work mostly for startups because that’s where the drone market is right now, and also for the educational academic world,” Hunsaker said. “Those two groups are where I see the biggest demand for a product like this. They are trying to design aircraft on the leading edge, and they need something like this right now.”
MachUp is free, open-source software. “When I was running my own company, I wanted to charge for it, but when I went into the academic world, I made the deliberate decision to make it open source,” Hunsaker said. “Enthusiasts can dig into the code to figure out what’s going on inside and why it works the way it does, and they can also make it better.”
The aim of MachUp was “to give the little guy access to this kind of software,” Hunsaker said. “Boeing, Lockheed, Airbus and other big aerospace companies all have their own in-house tools for developing aircraft that the average Joe doesn’t have access to without expensive licensing fees.”
Other Software
There are other free aircraft design software packages out there, such as AVL from MIT, “probably the most widely used tool that is the most similar,” Hunsaker said. “It’s very powerful, and used by a lot of designers. However, it’s all command-line interface, and requires a pretty significant learning curve to get into.”
Commercial aircraft design packages often analyze geometries using computational fluid dynamics (CFD) to analyze fluid flow over models. “The advantage of that is that you can handle extremely complicated geometries,” Hunsaker said. “The disadvantage is that it’s extremely slow and extremely computationally expensive, and it’s hard to automate. There are free versions of CFD code—NASA has CFD that U.S. citizens can use—but it’s extremely laborious to get solutions from it.”
In contrast, MachUp uses numerical lifting-line algorithms that can handle viscous effects. “These computations are much more simplistic—they’re not as high accuracy, but they’re extremely fast, and can give credible results for really low cost,” Hunsaker said. “With the initial design of the aircraft, you don’t need that high an accuracy—you just want a ballpark solution today rather than in two weeks.”
“Numerical lifting-line methods are versatile in their ability to handle complex nonlinear geometries for lifting surfaces, as long as the aspect ratios for the wing are higher than four or five,” aircraft designer Samuel Weiss said. The long, narrow wings of most passenger jets and light aircraft have an aspect ratio greater than four or five, whereas the short, wide wings of a plane such as the Concorde have a very low aspect ratio less than four or five.
MachUp code is much more limited in terms of computer-assisted design (CAD) capabilities than commercial packages. “It’s not a full CAD modeler,” Hunsaker said. “However, you can very easily create a model in seconds instead of hours.”
What Users Think
MachUp’s database of users suggest that nearly 3,000 users have signed up to make use of MachUp in the past two years, including people from dozens of companies and aerospace engineering departments and schools, such as MIT, Virginia Tech, and Embry-Riddle Aeronautical University, the world’s largest university specializing in aviation and aerospace. “We get people running about 30 simulations a day with MachUp, asking for aerodynamic data on a geometry.”
Robert Niewoehner, professor of aeronautics at the U.S. Naval Academy, has been using MachUp since this summer in his classes. “I’d written codes a decade ago for my students’ use, employing the same algorithms, but MachUp was much more advanced and flexible than my own,” Niewoehner said. “So I retired my own codes to use MachUp, and my undergraduate students are actively using it now.”
“It’s very flexible with geometries on the lifting surfaces, to include winglets, tailless designs, canards, multiple control surfaces, and so on,” Niewoehner said. “There’s no software to download, as the web version calculates solutions on the server end. Dr. Hunsaker has graciously made the software freely available for student and hobby use. Calculations are very fast, and results are easily exportable to MATLAB or simulation software. Dr. Hunsaker has also provided tutorial videos on his website, which successfully got my students up and running quickly.”
Samuel Weiss, now a mechanical engineer at Teal Drones in Utah, used MachUp for roughly three years. “I think it’s great,” Weiss said. “I use it whenever I’m at the beginning of a design cycle. I can create basic geometries and get basic analyses in a few minutes. I can quickly go through a dozen or more configurations and compare them all with each other. The ease of creating and analyzing geometries is great for the conceptual and creative part of the aircraft design process. And I can take screenshots to show people what designs look like in general terms instead of using 3-D modeling software like SolidWorks, which is more time-consuming.”
Weiss was lead aircraft designer and engineering manager at Utah State University’s AggieAir. While there he used MachUp to design an aircraft called BluJay, an aerial platform that weighed about 25 lbs., had a 10-foot wingspan, and could fly for about 3.5 hours on two lithium batteries. As director of flight testing and aircraft development at Vayu, Inc., in Michigan, he used MachUp “to develop a tandem-wing transition aircraft that could hover like a quadcopter and fly like an airplane,” Weiss said. He hopes to use MachUp at his new job at Teal.
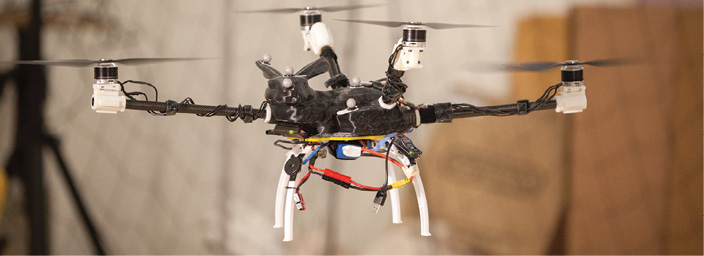
Jason Dorfman
Pending Improvements
Hunsaker noted that they have “lots of ideas to further improve MachUp.” For instance, “right now MachUp is good for designing fixed-wing aircraft, but can’t do quadrotor aircraft,” Hunsaker said. “We are working on it, though—we know quadrotors are of big interest in the drone world.”
In addition, “right now people can put a geometry into MachUp and hit analyze, and it will tell you the lift and drag and other factors of that airframe, but what people really want is a way to optimize the airframe, and we’re looking to streamline that process for users,” Hunsaker said. “Maybe instead of putting in a geometry, users can put in a mission profile—to carry a given payload at a given altitude at this velocity for a certain amount of time—and MachUp can provide a viable geometry that one can then tweak.”
“Another direction has to do with propellers,” Hunsaker said. “Until now, big players weren’t focused on drones, so there’s a need to improve predictions of aerodynamic performance at the slower speeds that drones operate at compared with the rest of the world of aerodynamics.”
All in all, Hunsaker hopes that drones have a bright future in front of them, in part due to MachUp. “A lot of people associate drones with killing things, but there are so many applications for drones other than that,” Hunsaker said.
“Once the public latches onto the power that unmanned aircraft offer to advance our lives, I think in the next 10 or 15 years, they’ll become far more prevalent and accepted.”