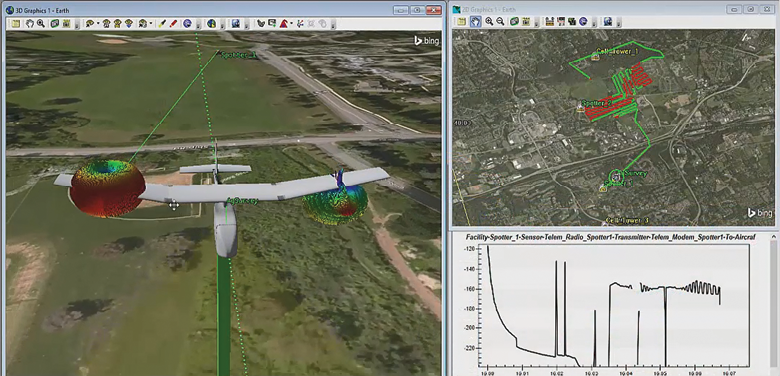
OneSky creating flight plans using existing route generation software called Aviator. Photo courtesy Lockheed Martin.
Decades of experience with satellite mission analysis, unmanned target control and “ruggedized” military test equipment enabled three firms to adapt their unmanned software and control systems for commercial operators across multiple domains.
The military legacy that underpins much of the unmanned industry comprises more than flight experience and cutting-edge hardware. It is shaped by software and flight control equipment whose reliability and advanced capabilities—like beyond-line-of-sight (BVLOS) operations—were proven while supporting military missions.
Today those control systems have evolved to serve commercial operators. Software created to map gaps in satellite communications and guide unmanned practice targets is now, decades later, evolving to become part of Unmanned Traffic Management (UTM) systems. One firm that ruggedized testing equipment to withstand hard use by the U.S. Marines is now building drone flight controllers to last for years in harsh environments like chemical plants.
ONESKY
The UTM system being developed by OneSky got its start in 1989, when three engineers left GE Aerospace to launch Analytical Graphics, Inc. (AGI) and develop the Satellite Tool Kit. The STK software package could calculate orbits and determine when a spacecraft would be in a position to communicate with ground stations.
Over the years, AGI steadily added new modules and expanded STK’s capabilities. Some in the U.S. military adopted the software to do real-time, 3-D visualization, enabling defense officials to envision air, land and sea forces as well as the space component. To reflect its growing versatility the name was changed to the Systems Tool Kit, which some 700 to 800 organizations now use, said Chris Kucera, the Exton, Pennsylvania, firm’s director of strategic partnerships.
STK is a modeling, simulation and planning application geared towards analyzing dynamic missions, said Kucera. For a space shuttle launch, for example, STK could be used to determine the many different communication and tracking systems that all have to work. “We can model those in advance and make sure that the infrastructure is in place to gather the data that we need.”
Those capabilities are now being used by AGI subsidiary OneSky to analyze the infrastructure supporting lengthy drone missions. For example, STK can determine if there are times and places along a planned flight route where a drone’s accuracy could be impacted by a limited view of navigation satellites. In that case, STK would analyze the satellites’ orbits and the terrain along the route for the planned date and time of the mission. But those are just a few of the factors that need to be noted. You need to know the weather along the route, Kucera said. If you are using cellular networks to communicate with and control your unmanned aircraft system (UAS) you need to be sure there’s cell coverage in place to support that.
“Just because I plan the flight from here to there doesn’t mean that I have the ability to communicate with [the drone] along that route,” Kucera said. “Cellular is not everywhere. GPS is not everywhere. Surveillance, like radar, isn’t everywhere—and so we have to model it to figure out where it’s available.”
ANALYSIS-BASED UTM
That kind of analysis, which Kucera says is currently missing in UTM plans, is at the heart of OneSky’s bid to become a UTM Service Supplier (USS). If you’ve modeled the elements needed along the route of an extended mission—such as communications and navigation—there is greater certainty you will have what you need to support a safe flight. Kucera said, “It feeds a safety and risk management process” that can be used to demonstrate to the FAA that you can so this safely.
In time, he said, the goal is to establish a process where such analysis supports automated approval of BVLOS operations.
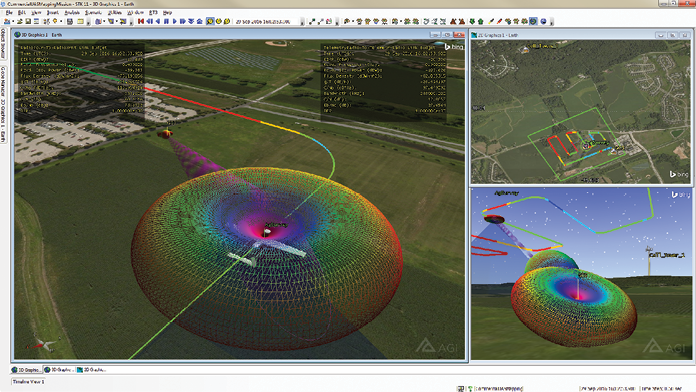
OneSky software modeling the command and control link along planned aircraft route. Photo courtesy Lockheed Martin
OneSky already has a contract to build a UTM system for Singapore, Kucera said, and its technology is being used by a number of drone test ranges. It recently completed live flight testing of its UTM system with NUAIR, which manages the FAA UAS test range at Griffiss International Airport in Rome, New York. The test at Griffiss, the first such flight at an FAA UAS test site, validated NASA Technical Capability Level 4 and the USS-to-USS integration protocol.
“The ability for multiple UAS services suppliers to communicate with each other is another key element in implementing a UAS traffic management system that can facilitate beyond visual line of sightt commercial operations,” said Tony Basile, chief operations officer at NUAIR, in a statement. “OneSky has differentiated themselves by demonstrating their ability to deliver robust UTM capability to support BVLOS and urban operations. We especially appreciate the analytical depth of their software as well as their exceptional support.”
VCSI
Where STK got its start with satellites, CDL Systems’ vehicle control station—that is, VCS—began as the controller for an unmanned boat called the Barracuda that served as a Canadian Navy practice target in the 1990s. Lockheed Martin Canada has since acquired CDL and the software is now being used by the U.S. Army on a number of its systems, as well as by a yet-to-be-announced commercial customer.
“Our core business has always been unmanned vehicle control,” said Dustin Engen, the Calgary, Alberta, firm’s business development manager. “So, over the last 25 years the software that CDL Systems has produced has over 1.5 million flight hours across about 40 vehicles, the bulk of which is [on] the U.S. Army’s common controller.”
That controller, the Universal Ground Control Station (UGCS), is used to fly the Army’s three primary, larger UAS—the Hunter, the Grey Eagle and the Shadow.
The next generation of that Army software is now being offered commercially. Called VCSi—the “i” is for international—it has already been chosen by a company for a new High Altitude Long Endurance (HALE) drone being tested this summer. CDL is under a nondisclosure agreement, but Engen did say the UAS company was using the software to control four or more multiple drones at the same time.
Such multi-drone operations are “very much aligned with where the market’s going,” said Engen. “A lot of the historical stations you’ll see are very much designed around one or even multiple operators controlling a single vehicle. And this commercial customer is using VCSi to control multiple vehicles from a common controller for long periods of time.”
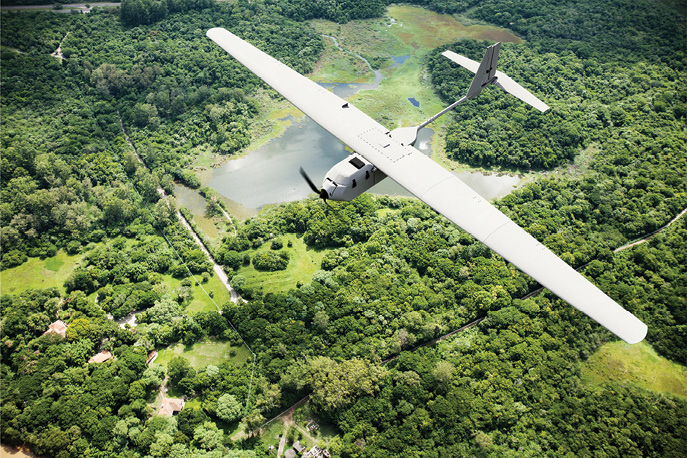
VCSi can control a fixed-wing drone like Lockheed Martin’s Condor, which is used for ISR and targeting support. Photo courtesy CDL Systems
At least one other user is trying VCSi for multi-drone control — it is flying four UAS at a time. But VCSi has the capability to expand that number substantially. In fact, Engen said, the software could support a drone-based delivery service or swarms of UAS doing pipeline inspections.
The key is the management-by-exception approach being used in the VCSi software. Where human pilots are now very directly involved in flying UAS, VCSi will allow a vehicle to proceed with pre-programmed missions or tasks, having the operator step in only if an issue arises.
“So we built the user interface to enable one operator to be really effective with a lot of drones. So a future use case you might envision is a delivery drone that is receiving automated mission plans from some system and VCSi could be acting as that manager or supervisor console where they largely undertake the tasks—and the user steps in only when something’s wrong or human input is required,” Engen said.
MULTI-DOMAIN CONTROL
VCSi’s versatility extends beyond handling multiple drones to managing multiple kinds of unmanned vehicles. That is, the software can control ground and surface marine vehicles—all with the same hardware.
Developing a common controller addresses some of the practical challenges of training time and space. Training time can not only be reduced but the same number of trained staff can be more versatile across systems and they won’t need to set up a room full of different kinds of stations to deal with a large multi-domain operation.
Having one control station for marine, land and air vehicles also brings together all the data into a single place and gives the operator a much better picture of what’s going on. During an event, for example, an unmanned aircraft could capture the big picture from overhead, enabling the operator to identify critical areas and then send automated boats or ground equipment to take samples or provide support.
Though multi-domain efforts are still uncommon in the commercial world, R&D programs are beginning to emerge in the military. NATO in particular is looking at what would be involved in developing a multi-domain control station. CDL is on the committee working on that future standard, Engen said.
CDL sees multi-domain systems as a growth area, said Engen. “I think this need will become sort of amplified. People will just simply need to bring it all from a common piece of software and won’t want to deal with that many different controllers.”
CDL is also planning to offer VCSi as a local traffic manager for UTM systems. The software will bring in FAA-type data like aircraft location information, waypoints, information on other aircraft and data on non-cooperative traffic from radar or other sensing systems. This information would be combined to give a comprehensive picture of activity in the area.
“[It’ll] allow a manager or a controller to sort of see how their drone or their vehicles are interacting,” said Engen. The capability, he added, might be available as early as 2020.
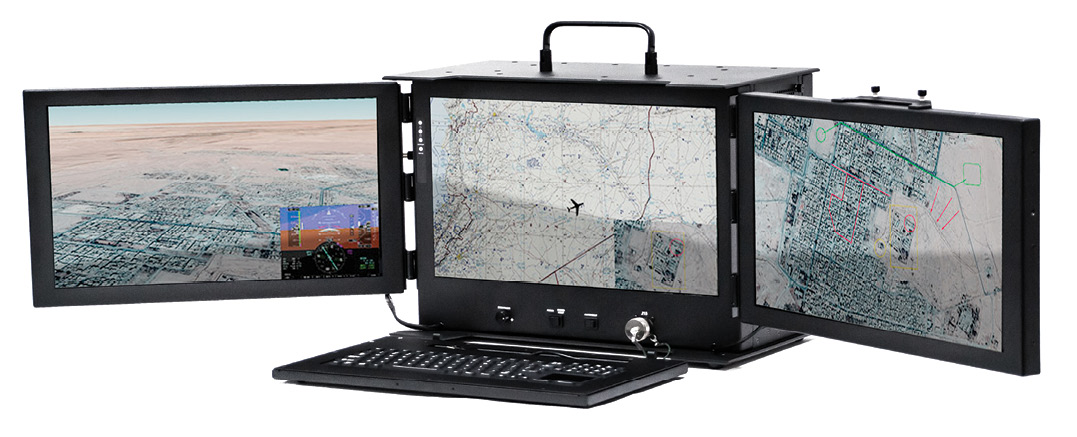
CP Technologies’ Ruggedized Portable Photo courtesy CP Technologies
RUGGEDIZED PORTABLE
Combat Proven (CP) Technologies puts everything it’s learned building equipment for the U.S. Marines into its battle-tough drone control stations. The company has created hardware that is easier to use in bright sunlight, can withstand most of Mother Nature’s worst tantrums and is “future proof” for long stretches of time.
The San Diego, California-based company got its start 23 years ago building a single-screen version of its current equipment that the Marines used as a test station for assessing the electronic systems on its light armored vehicle, the LAV-2. Though CP Technologies did not start out planning to build drone control stations, its team saw an opportunity to address the problems UAS operators were having with off-the-shelf controllers like tablets and laptops.
“They’d take a commercial display with a processor, stick it a Pelican case and then try to operate it out in the field—and a lot of the screens weren’t direct-sunlight readable. They weren’t ruggedized. They didn’t survive for long. Laptops didn’t have the processing power or the screen capability to be able to fly a UAV,” said Michael McCormack, CP Technologies’ president and CEO. “And we realized that the processing power of [our] system allowed it to be utilized for more than just a test station.”
The system they created is as utilitarian as its name. The internal components are shock-mounted to withstand vibration, temperature and humidity. The three-screen system is also completely sealed and can be used in rain or snow—pretty much any environment, said McCormack. “So, whether you’re sitting out at a chemical plant or you’re sitting out in the middle of an oil field or a very harsh environment, you have this very ruggedized system that can take dust, dirt, moisture, whatever you throw at it. But on top of that you have direct-sunlight-readable screens as well. So if you’re out there using it as the ground control station it’s going to provide very good visibility and also a lot of processing power and a lot of human interface to be able to see the information that’s coming off the aircraft.”
It is the toughness and the processing power that led Dow Chemical operators to choose Ruggedized Portables, McCormack said. They were doing aerial surveying of their equipment and their infrastructure—controlling the UAS using a laptop, he said. The environment was hard on equipment and they had to take the data back to the office to process it. With the Ruggedized Portable they’re able to do all that work on site instead.
The Portable’s internal components are modified off-the-shelf systems that are chosen based on the customer’s needs, and the operating system is completely user-definable. It comes loaded on the system, ready for the users to add their own software.
“What we’re not doing is redesigning all the technology in the world,” said McCormack. “We’re taking existing technology and packaging it in a survivable platform.”
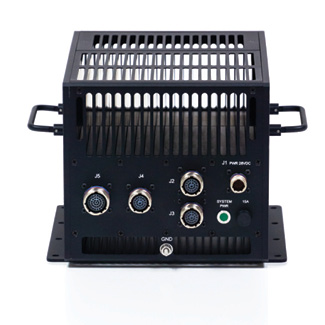
Mission Computer Photo courtesy CP Technologies
FUTURE-PROOFING
What the company does add to the hardware is the ability to dramatically limit the number of times it has to be updated. By plugging into the plans of the component manufacturers, CP Technologies is able provide “revision control”—that is, anticipate and address the revisions planned for certain components and work around those changes.
“The end user’s the one who’s defining the software. They don’t want that software to have to be updated all the time because your memory changes or your processor changes—and that’s what people typically have to do when they’re using commercial-grade systems,” McCormack said.
“We’re an Intel platinum partner so we can see the road maps that Intel is going to have out there for the next five to eight years,” said McCormack. “So we know if a processor that they’re going to be building, it’s going to be available in eight years.”
For parts that aren’t designed to last that long, CP Technologies will find an exact replacement when the part fails, make sure that the customer signs off on it and then revision the part number up to the next revision.
“So we can give you a processor that’ll be good for 8 to 10 years,” said McCormack. “We can give you a motherboard—you know we do Navy programs—we’re providing motherboards out there that are good for 15 years. So the first thing we need to understand from the customer, that we always talk to them about, is, ‘Hey, how long do you need this program to be fixed for?’”