Inspecting and mapping indoor or underground locations where GPS isn’t available calls for unmanned aircraft with unique designs that let them find their way without the benefit of satellite positioning.
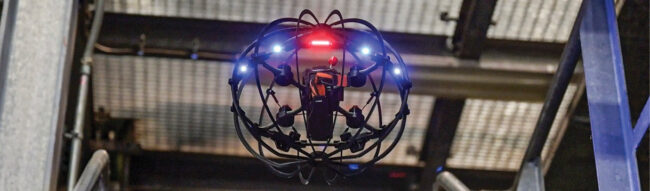
Photo courtesy of Skypersonic.
Troy, Michigan-based Skypersonic, owned by San Juan, Puerto Rico-based Red Cat Holdings Inc., already had a drone that would fly without benefit of GPS. Now they have one that flies with a pilot on the other side of the world.
Skypersonic’s Skycopter is part of a niche of the drone market that serves GPS-denied environments. These are places, such as inside buildings, mines, sewer systems, silos, oil and gas platforms or storage tanks, where a signal from a GPS satellite is blocked or unreliable, yet there is a need for precise mapping and inspections. Generally, these places are dangerous, unpleasant or hard to reach, and the work is slow.
Drones that work in this space rely on a combination of cameras, sensor arrays and software to “know where they are” in relation to their surroundings and to provide highly accurate images of challenging indoor environments. They usually communicate by radio with their pilots, and can be outfitted with payload components to suit the job at hand.
The Skycopter, for example, uses a 1080p tiltable camera and can be outfitted with sensors such as an on-board radiation detector. It is powered by a lithium-polymer battery with a flight time of 12 minutes, weighs 2.9 pounds, has a diameter of 13.8 inches and can operate at temperatures ranging from -20 to 40 degrees Celsius. It can fly in complete darkness using an ultra-bright 360-degree LED system. Like others in this category, it is “caged,” that is, surrounded by an enclosure to avoid damage to or from the rotors.
While some GPS-deprived drones use artificial intelligence to help maneuver, Skycopter’s use of AI is limited. Giuseppe Santangelo, founder and CEO of Skypersonic, said, “we consider some kind of inspections too complex—there could be dust, and obstacles that AI isn’t able to do yet.” Plus, “it might involve a specific area that only the human would know how to do,” he added. “We use AI to assist, but the pilot is always in charge.”
Skycopter also doesn’t use LiDAR, which many of its competitors do, because of the weight penalty. “Good LiDAR is heavy,” said Giuliano Golfieri, Skypersonic’s chief pilot.
Skycopter has been used to inspect the inside of a nuclear plant, replacing two people and eliminating the need for scaffolding; inside an industrial chimney, eliminating the need to shutdown while people repel on ropes; inside an industrial boiler, avoiding a shutdown while scaffolding is erected inside the boiler; on a manufacturing floor, eliminating the need for a shutdown and providing access to places people can’t reach, even with scaffolding and scissor lifts. It’s also been used in reconnaissance for the military and in search and rescue missions.
Last year, Skypersonic showed off a relatively new capability using the Skycopter. In a demonstration, using only a cell phone and an internet connection, a Skycopter pilot visually inspected the interior of an operational utility plant in Turin, Italy, using a drone controlled from Orlando, Florida, 4,800 miles away.
Santangelo said the development of this cell phone/internet long-distance capability came about “not out of inspiration, but desperation,” because of COVID. Skypersonic usually sent a trainer to client companies. With everyone grounded, the inability to train was a serious threat to the business.
So, the company went to work. First, they designed a simulator. Then they developed the long-distance system.
“The key is our software,” Santangelo said. “It uses a multi-point network—the internet—to create a point-to-point system with low latency. Then we created visual compression video software that would work with the limited bandwidth we utilized, to keep the latency low.”
Golfieri, based in Italy, where Skypersonic has its European office, headed the Orlando-Turin mission and was onsite in Turin as a failsafe. “We were surprised at how well this worked,” he said. “There was only a tenth of a second of latency.” Recently, he added, they have been able to train and certify pilots at a distance as well.
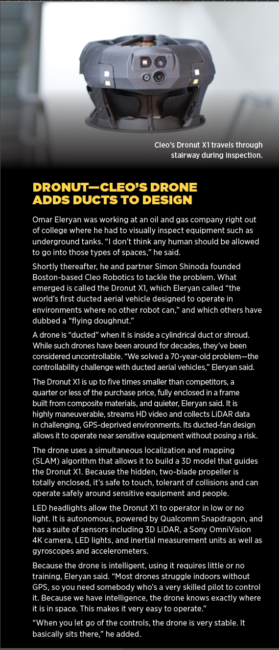
A GROWTH MARKET
The market for these drones is growing rapidly and is potentially very large. Indoor locations in need of inspections are literally everywhere, such as:
- Assets including pressure vessels, storage tanks, silos, bins, boilers, nuclear reactors and FCC units
- Factories, particularly ceiling installations and within and around machinery. These become complicated as businesses try to minimize downtime, because it’s often necessary to close sections of a plant floor during the inspection as a precaution. Small drones that can operate safely while people continue to work can be particularly valuable here
- Maritime vessels where fuel tanks and cargo holds can be deep within a ship, metal can interfere with GPS, and it can be dangerous for people to work
- Mining operations where crumbling rock and dust interfere with GPS
- Critical infrastructure installations such as in military bases, power plants, dams, and nuclear plants. Locations within these can be hard to reach, dangerous to approach, or both
- Tanks in pharmaceutical, food, cosmetics and other industries
- Damage sites, such as after fires and hurricanes, where large debris can interfere with GPS and the inspection includes indoor as well as outdoor areas.
PSYCHOLOGICAL HURDLE
A key sales hurdle, according to those selling the systems, is overcoming a potential customer’s long-held belief that a drone image can’t deliver the kind of detail needed for inspection or mapping tasks, especially when it comes to crucial jobs such as finding a hairline crack in a foundation.
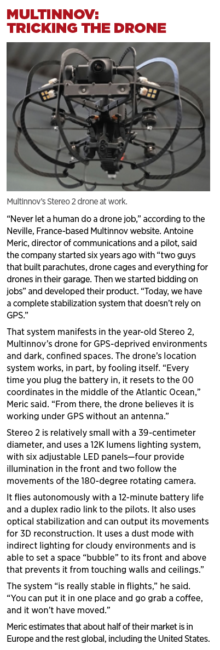
While the opposite is usually true, it usually takes time, demonstrations and comparisons to prove to a customer that a drone might actually do a better, faster, safer and cheaper job than a person covering the same territory.
DRONES IN CAGES
Most drones developed for GPS-denied environments are made to fly in the dark in complex environments. In spite of powerful LED lights, various sensors and LiDAR, and resulting 2D and 3D image models, the operator may not be able to avoid touching various outcroppings. This means the drone and its payload is usually encased in a round “cage” designed to protect the drone rotors and payload from obstacles, and, in turn, protecting whatever is being inspected from the rotors. Usually, these surroundings are made of metal with the drone and its payload visible within, although a solid, opaque casing can be used as well.
BATTERY LIFE
For drone operators used to “outdoor” drones, some of which can fly for hours, the battery life on today’s GPS-deprived caged drones is short—usually in the realm of 12 to 14 minutes. This is mostly because these drones are smaller to get into tight spaces, so the batteries are also smaller. Manufacturers and operators report this is almost always enough time to complete the task at hand, however. If more time is needed, a relay system can be set up.
THE INDUSTRY IS YOUNG
Most GPS-deprived drone companies we spoke with were five or six years old or less. These first generation “pioneers” herald a move from human to drone survey and inspection in the years ahead, even in hard-to-reach areas. And beyond visual line of sight regulations don’t apply to the indoor use of GPS-deprived drones, even if the drone flies into a piece of ductwork, behind a boiler, or is otherwise out of view of the pilot, because they are not flying in open airspace.
All in all, while GPS-deprived drones fly into small spaces, they are destined to make a big impact.
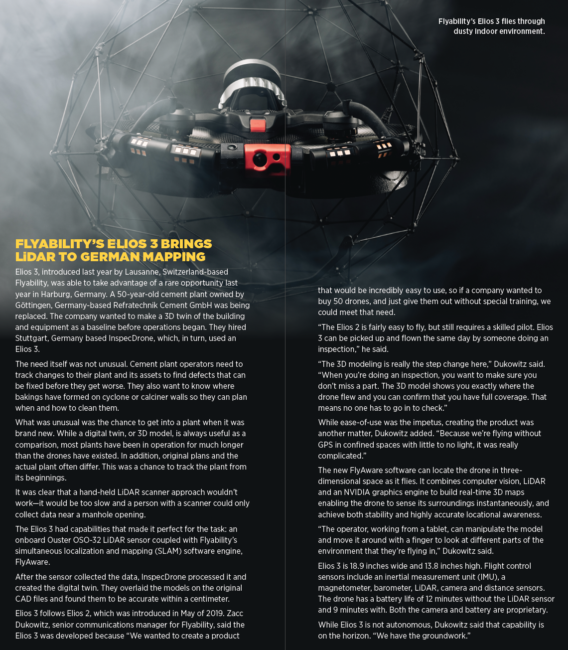